US project updates, Evonik to sell methacrylates business, ACC urges CFATS extension
Our pick of the latest petrochemical news you need to know
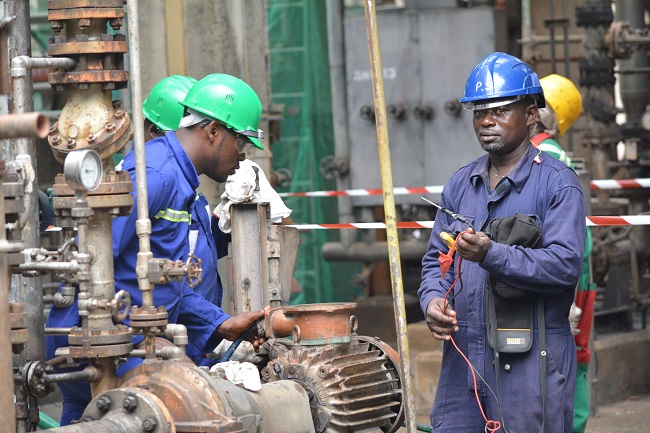
ExxonMobil advances polyolefins expansion in LA
ExxonMobil will invest in a polyolefins expansion in Baton Rouge, Louisiana which will likely cost over $500 million.
Construction on the expansion will begin in 2019, and the project is expected to add 45 permanent jobs, 20 permanent contractor jobs and support 600 temporary construction workers.
The project will add a new polypropylene line with a capacity of 450,000 tonnes/year and is expected to start up in 2021.
Exxon in 2018 won unanimous approval from Louisiana state and local officials on a tax break worth an estimated $31.7 million over a decade for the polyolefins expansion, through the state’s Industrial Tax Exemption Program. Because of recent reforms, the company is required to pay 20 percent of the property tax bill on the expansion despite the exemption.
In addition to the ITEP exemption, Exxon is expected to get Enterprise Zone incentives and will use Louisiana Economic Development's FastStart workforce training program.
Demand for chemicals continues to surge and is driving the company's $20 billion worth of investments along the Gulf of Mexico.
“Growth in feedstock supply along with the increase in global demand for chemical products continues to drive our strategic investments and expansion along the Gulf Coast,” ExxonMobil Chemical President John Verity said in a statement. “We’re well positioned to meet the demand for these high-performance products and investing further in Baton Rouge enhances our facility’s competitiveness.”
The engineering, procurement and construction contract for the project has been awarded to Baton Rouge-based Turner Industries and Jacobs Engineering, with ExxonMobil saying the companies will use local workers to design and construct the new facility.
Bayport Polymers begins building PE plant in TX
Bayport Polymers, has broken ground on a polyethylene plant in Pasadena, Texas, that will have an annual capacity of 625,000 tonnes/year and is set to open in 2021.
Also called Baystar, the project is a 50/50 joint venture with Total Petrochemicals & Refining USA and Novealis Holdings LLC. Novealis is co-owned by Borealis AG of Vienna and NOVA Chemicals of Calgary.
The project will create about 1,750 jobs at peak construction. The unit is expected to start up in 2021 using Baystar's new "Borstar" technology.
$220 million expansion coming to DuPont specialty films site
DuPont is planning a $220 million expansion at its specialty films facility in Circleville, Ohio, increasing the production of Kapton polyimide film and Pyralux flexible circuit materials. The project will likely launch by 2021 and will position DuPont to meet growing demand in automotive, consumer electronics, telecom, and defense.
DuPont expects the new assets to be operational by 2021.
“Our new production assets will position us well to support the growing need across many sectors for our advanced high-reliability materials for innovations in areas such as 5G, automotive, flexible displays and artificial intelligence, said Jim Fahey, president of DuPont’s electronics and imaging division.
DuPont has been making Kapton polyimide films for over 50 years.
DuPont’s electronics and imaging business is part of the new specialty products division of DowDuPont, and was created by the 2017 merger of Dow and DuPont, and is a combination of Dow’s electronic materials and DuPont’s electronics and communications businesses.
Evonik to sell methacrylates business to Advent
Evonik agreed to sell its methacrylates business to U.S. private equity firm Advent International for €3 billion.
The selling price is 8.5 times the business’ EBITDA and the transaction will be subject to approval.
The transaction includes the Methacrylates, Acrylic Products and CyPlus business lines, as well as some methacrylate resins activities, and is expected to close in the third quarter.
The methacrylates business has 18 production sites and 3,900 employees worldwide. It generated an average annual earnings before interest, taxes, depreciation and amortisation (EBITDA) of about €350m and sales of about €1.8bn/year in 2016-2018 and expects similar levels for 2019.
Evonik will use the sale proceeds to strengthen its balance sheet and, above all, for targeted growth projects. That includes funding the purchase price of the U.S. company PeroxyChem, which Evonik plans to close in 2019. In addition, some funds will be used to strengthen the present specialty chemicals portfolio.
ACC urges congress to support multi-year extension of chemical security regulations
Congress should support the ongoing effort to safeguard chemical facilities and provide much needed stability to one of the nation’s anti-terrorism programs, according to an industry exuctive.
Kirsten Meskill, Director of Corporate Security for the BASF Corporation testified on March 12, 2019 on behalf of the American Chemistry Council (ACC) before the House Committee on Homeland Security Subcommittee on Cybersecurity, Infrastructure Protection and Innovation.
“ACC supports a long-term reauthorization of the Chemical Facility Anti-Terrorism Standards (CFATS) program. Ensuring that CFATS remains in place is a crucial part of establishing a stable regulatory environment and providing the needed certainty to foster long-term security investments,” said Meskill.
CFATS has proven to be well-suited for regulating security because it is able to account for the diverse nature of facilities that manufacture, use or store chemicals and the unique challenges each facility faces while ensuring they have measures in place to address wide-array of security standards.
“Over the past few years, the Department of Homeland Security (DHS) has significantly improved its administration of the CFATS program; having a positive impact on chemical security across the United States. Several factors have led to its recent success, including: Improved site security inspections; improved risk assessment; and, a more streamlined and consistent Site Security Plan (SSP) authorization process,” Meskill continued. “Most importantly, DHS leadership has demonstrated a willingness and commitment to work with the regulated community to help improve the program.”
Recognizing that there is still room for further improvement to CFATS, Meskill concluded her testimony by offering several specific recommendations, including limiting worker screening against the terrorist database to high risk facilities to help reduce the risk of putting sensitive personal data at risk; improving the transparency of the program – particularly relating to the process of tiering facilities; and creating an industry stewardship recognition program that will help incentivize operators to go beyond regulatory compliance.
In addition to offering suggested improvements, Meskill underscored that the primary goal of CFATS must not be compromised.
“It is also important that CFATS maintain its security focus,” she said. “The continued success of the CFATS program will depend upon its ability to help manage security risks. CFATS should not stray into areas outside of its primary function of addressing security risks and into areas already addressed by well-established environmental and safety regulatory programs administered by other federal and state agencies. Layering on additional responsibilities could impair its focus and will impede its progress toward the goal of protecting important critical infrastructure from security threats.”
Wax Market worth over $10 bn by 2024
The wax market is forecast to exceed $10 billion in 2024; according to Global Market Insights, Inc.
Sturdy growth in cosmetics and the personal care industry are expected to drive wax market demand.
Wax has air and water barrier properties, which make it beneficial for packaging, cosmetics and adhesives.
Increasing product applications in the packaging sector will also be a key factor for the wax market growth.
The global packaging industry is primarily driven by the BRICS market which accounts for approximately 37% of the global demand. The packaging industry growth in Asia Pacific is mainly a result of increasing consumption of consumer goods, which in turn has driven the need for sophisticated packaging.
In 2016, the packaging segment accounted for a prominent share of the overall wax market. The product has extensive usage in paper and food packaging to provide extra protection against foreign odors and moisture.
Paraffin wax held the largest share in the petroleum and mineral wax category in 2016. Major applications of this product include electric insulation, candles and lubrication. Demand for paraffin wax has been gradually increasing since 2013 and is likely to rise at a steady pace.
In 2016, Asia Pacific was the largest region, by volume and revenue in the global wax market. Asia Pacific was followed by Europe for volume.
Major companies operating in the wax market which are highly integrated are China National Petroleum Corporation, Exxon Mobil, International Group, Royal Dutch Shell PLC and Sinopec Limited.