What’s new about gravity base foundations for offshore wind?
WindEnergyUpdate speaks to Petter Karal, CEO of offshore wind turbine foundation technology provider, Seatower, to learn how the latest gravity base foundations resolve installation issues that have plagued the offshore wind industry to date.
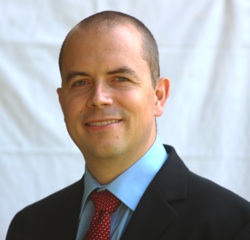
Interview by Rikki Stancich
Gravity base foundations have been used for years in the offshore oil and gas industry. A variation has already been used at Thornton Bank and gravity base foundations have been slated for several for Round 3 projects.
So what is exciting about the latest gravity base foundation to hit the market? More importantly, what sets it apart from the other foundation options currently on the table?
There are several points that make Seatower's foundations worth sitting up and taking notice: Firstly, Norwegian wind turbine foundation technology provider, Seatower, has developed a low cost solution for quayside mass-manufacture and assembly of the foundations.
Secondly, the installation process does not require specialist vessels and is resiliant in North Sea weather conditions.
To top it off, the environmental impact throughout the foundation’s lifecycle is minimal, with no sea bed preparation requirement and no trace of the foundation post-decommissioning.
WindEnergyUpdate speaks to Petter Karal, Seatower’s CEO, to learn more about the latest offshore foundation solution.
WindEnergyUpdate: Seatower has developed self-installing gravity bases for offshore wind. The technology has been used – and proven - in the offshore oil and gas industry. How does the technology differ for use in the offshore wind sector?
Petter Karal: We believe this is the biggest R&D undertaking into offshore wind foundations ever. There are many differences between the requirements of building a huge one-off oil installation in 400 metre deep Fjords, and for mass-production in facilities close to European offshore wind farms. The logistics and the value chain processes are dramatically different.
When you are talking about mass-producing the gravity bases for a range of water depths at a range of locations - East and West UK, Germany, France, and Netherlands - you need to be able to build at site. However, the facilities at the quayside are very different, as is the draft available, which requires some new bottom-up thinking.
The load requirements are also very different – the load on a wind turbine is very different from the load on any given oil and gas topside. Typically, oil and gas platforms are designed for maximum load waves. The wind turbine and foundation on the other hand, are designed for fatigue and the effect of vibrations over a span of 20-25 years. There are also more overturning moments of load that affects the point high above the sea level.
So the design of the wind turbine foundation is driven by fatigue rather than maximum load.
The economics of building a one-off foundation for an oil and gas installation also has a different scope in terms of equipment and materials requirement. For offshore wind farms, the assembly line needs to be cost effective and materials need to be readily available (in other words, we need to use standard grade steel and concrete).
Seatower's Cranefree foundations are designed for quayside manufacturing and assembly
WindEnergyUpdate: When you talk about mass production, at what rate could the Cranefree turbine foundations be turned out and what are the major limiting factors?
Petter Karal: We are planning for building up to 200 foundations per year for one of the bigger Round 3 projects, which is equivalent to 100,000 tonnes of steel and 45,000 tonnes of concrete. This is a huge amount in terms of world supply.
The question is whether this can be freed up from other sources. If you started using special grade steel, you would almost certainly limit your access to supply.
Scalability is a very important aspect of the development process. We have heard potential customers discuss a peak rate of 10GW per year being installed (roughly 2000 turbines per year).
For this we would require a couple of thousand skilled welders - and I’m not even sure that there are even that many in the UK at present, so a big question is: Where will the skilled welders and other skilled workers come from?
WindEnergyUpdate: Seatower has developed a low-cost industrial process for the manufacture, assembly, and installation of gravity-base foundations. How much quayside land is required for the prefabricated steel sections to be stored and assembled?
Petter Karal: One of the main benefits of the concept is the fabrication and logistics side. We are flexible and adaptable, which takes out some of the risk. Our typical throughput (around 40-50 foundations per year), would require around 25 acres, or 100,000 metres squared. For one of the bigger Round 3 projects, you would require roughly three times the land space.
Compared to any other way of getting foundations built, our land requirement is modest. Furthermore, the land requirement doesn’t scale proportionally with the number of foundations – less of a buffer is required for higher throughput.
We also require a quayside where pre-fabricated steel could be delivered and a berth for the vessel that brings them.
On the drawing board we have plans to carry out the entire pre-fabrication and construction at the same plant in the UK. At one end we would have fabrication and at the other, assembly. We have a potential site capable of this.
WindEnergyUpdate: How does the Cranefree system allow for a bigger weather window for installation than you would normally have for conventional foundations?
Petter Karal: As the name suggests, no crane is required for the installation of these foundations. Most foundations to date have used cranes.
Our system can withstand any weather in the North Sea. The ocean tugs used for towing and installing the foundations are built to operate in harsh conditions, so the only limiting factor is when conditions are too rough to operate on deck of the tugs.
The Cranefree gravity bases can be towed to site using standard tugs
When using cranes, it is a delicate and risky operation, with very low tolerance for high waves and rough conditions.
The advantage of our system that you only need a good forecast 12 hours ahead, so you have a short weather window – the advantage of which is that short good weather windows occur more frequently than the longer (good) weather windows required for crane installations.
Also, longer weather windows require a higher safety margin. For instance if your wave tolerance is 2m and your operation takes 72 hours, the rules say you need a 72-hour forecast of less than 1m waves to proceed. If your operation takes only 12 hours, the rules allow you to start if 1.5m waves have been forecast.
The installation operation with the crane-free system usually takes less than 12 hours from positioning to the skirts have been fully embedded in the seabed.
WindEnergyUpdate: Seatower’s gravity-base foundations do not require seabed preparation. What environmental and financial advantage does this confer?
Petter Karal: When you dredge the seabed you disturb the benthos, which is the marine life in the topsoil, and this destroys habitats. You incur a lot of costs relating to offshore dredging equipment, as well as weather delays, all of which increase the risk of the project.
Putting down a gravel bed is costly and risky as well. Some gravity bases require gravel beds up to the size of a soccer pitch. It needs to be very precisely laid and has no environmental advantage.
When driving piles, the subsea noise from the hammers disturbes marine mammals, spawning herring and other ocean life. Above water noise can create near-shore disturbance.
Regulators are increasingly concerned about the environmental impact of large-scale pile hammering, and developers are increasingly facing restrictions on this activity. The operation also adds cost and risk to the project.
WindEnergyUpdate: What maximum water depth is the Cranefree foundation designed for?
Petter Karal: The Cranefree Gravity is economical down to about 50 metres water depth. However, we have ways to build cost-efficiently down to as much as 100 metres based on Cranefree technology.
WindEnergyUpdate: While the foundation technology is crane free, the turbine installation phase is not. Is Seatower working on solutions for quayside assembly of both the foundation and turbine? If not, why?
Petter Karal: This is a very interesting question. We have been working on such solutions and have come up with conceptual designs. However, our main customers don’t see a big benefit in the combination, citing several reasons:
Firstly, current turbine installation methods are not as big a cost-driver as foundation installation. Foundation installation costs 2.5 – 3 times more than the turbine installation.
Installation of a tower and a turbine is much more standardized than the installation operation of foundations, which need to be adapted to seabeds and other local conditions. Turbine installation is far more homogenous and the work takes place above water.
Secondly, the turbines that are available in the marketplace now and in the coming years are not designed for the movements and tilt of being transported in pre-installed condition.
Third, customers specify that they prefer the contracts (for turbine and foundation installation) to remain separable.
And fourth, the dependency that would be created between the supply of the turbine and foundation does not appeal to the customer. Both the turbine logistics and the foundation logistics are enough of a challenge separately. Intertwining the two projects would increase their complexity and make both more vulnerable to delays.
There are so many reasons why you don’t want to go there and our customers have asked us not to.
WindEnergyUpdate: When it comes to decommissioning, what are the advantages of gravity-base foundations over other foundations?
Petter Karal: In the oil and gas sector, decommissioning is costly and is a real pain in the neck. The only good thing about it is that the cost is so far in the future that in the financial models the cost diminishes due to the interest rates. So a decommissioning plan is important.
With the Cranefree gravity-base foundations, the decommissioning concept is straightforward. You pump the sand out; pump the water out; the foundation becomes buoyant, floats to surface and is towed to shore. So you have the means of lifting and moving the foundations only using tugs and pumps.
The traditional foundations used in offshore wind and oil and gas require cranes and cutting technologies. For example, to decommission the concrete gravity foundation used at Thornton Bank they will probably require a crane and they will be left with a 3000 tonne piece of concrete.
We will take our foundation with us, including the concrete injected between the skirt and the seabed if required. All that will be left behind is the rock used for scour protection, but we are already looking into ways to deal with this as well.
WindEnergyUpdate: Where have Seatower's foundations been deployed?
Petter Karal: None of Seatower’s crane free gravity base foundations have been installed yet, however, many gravity base foundations that have been installed to date, such as the Condeeps – around 20 have been installed. In that sense, the technology is proven.
We expect to see orders in the next 3 – 15 months.
To respond to this article, please write to the editor:
Rikki Stancich: rstancich@gmail.com
All images courtesy of Seatower.