Rotor blades: why ignoring them could bring considerable risk
Entities that do not have a strong focus within their long term operation plan on their rotor blades are accepting potentially considerable risk. We look at how operators can turn that around and prepare for post warranty costs.
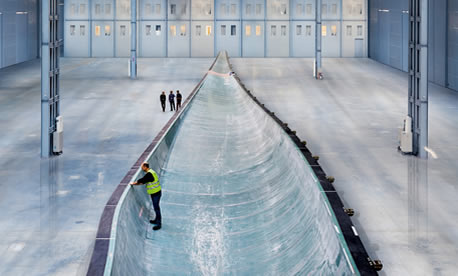
By Ritesh Gupta
Information about the state of the rotor blades prior to post warranty operations is crucial to being able to better evaluate post warranty costs.
But generally, such information is not completely attained until end of warranty. Being aware of the condition of the rotor blades at the time of project initiation is advantageous for setting a benchmark for assessing the condition at end of warranty. There are several alternatives for the owner/ operator to work on this. It could be in-factory inspection of manufacturing facility before or during rotor blade construction or on-site incoming scrutiny of rotor blades prior to construction. And timing is significant, too, in this case. While working on such evaluation, one needs to work out adequate time for being able to react to the inspection conclusions.
Also, an appraisal of original equipment manufacturers’ O&M records should be done. Plus, there is a need to look at continuous monitoring system (CMS) reports, too, if possible. Such examination will underline the prevailing trends in maintenance and inspection which can then be weighted up, as well as offer a record to reference against the findings from end of warranty inspections.
Once the condition of the rotor blades is comprehended, a detailed assessment can be done on the route chosen for post-warranty operations and maintenance.
Choice can be made from following options - in-house service, independent service provider and OEM.
Continuous improvement
The industry is targeting sustained improvement in this arena in order to be truly cost effective. In November 2013, Alstom achieved a major milestone in the offshore wind sector as it installed the 6 MW Haliade 150, off Ostend harbour at the Belwind site in Belgium. It is being highlighted that owing to its 150m rotor (with blades stretching 73.50 metre), the turbine is more efficient since its yield is 15% better than existing offshore turbines. It operates without a gearbox, using direct drive.
Chris Wraith, engineer, Complete Wind Corporation says rotor blades are very large, and ever growing, components, generally manufactured with very minimal automation. It should be noted that this leads to considerable component-to-component manufacture variation.
“The engineers that have designed this and are designing the next generation wind turbine rotor blades have been and are being forced to ask more and more of their materials and manufacturer invariability due to the non-linear scaling factors associated with larger rotor blades,” says Wraith.
Coupled with an apparent deficiency within the fatigue testing procedures to properly test for the environmental factors associated with wind turbine rotor blade operation, owners and operators that do not have a strong focus within their long term operation plan on their rotor blades are accepting potentially considerable risk.
By understanding the condition of the rotor blades prior to post warranty, the owners and operators are provided with a feedback mechanism which can be used to evaluate their pro forma O&M cost model. Whereas as most manufacturing and transportation related defects/ anomalies present themselves in a bathtub shaped function (highest at the beginning and the end of the wind farm life), wear related defects tend to follow an exponentially increasing function.
Early discovery and repair of these defects will have a great effect on controlling post warranty O&M costs, says Wraith.
Being ready
Matthias Brandt, director of Deutsche Windtechnik says, “In terms of maintenance mostly the blades are not a critical part of a wind turbine but if something happens you better be ready. One-fifth to one-quarter of the costs of a wind power plant are caused by the rotor blades and therefore a good long term maintenance concept is crucial.”
One of Deutsche Windtechnik’s main resources is the experience of its technicians and engineers. The entity has a wide range of different experts and a specific department which concentrates exclusively on rotor blades.
Reducing risk of losses
Owners/ operators need to finalise a thorough and effective inspection and maintenance programme (this initiative can be based on the suggestion of the specific OEM, and amended as per the findings from EoW and earlier research discussions):In addition to coming to grips with the condition of the rotor blades at end of warranty, one can work out the expected future repairs based on an assessment of the local conditions; Rely on interaction with other owners/ operators of the same kind, as well as in-house and ISP expertise; Entities also need to plan appropriate repair procedures and that the repairs done are of adequate quality. If this is not the case then chances are that owners and operators might end up facing future re-repair costs.
Early detection of minor defects allows for re-inspection and/or repair to be listed as part of scheduled maintenance and during the most helpful weather conditions, thereby reducing turbine down-time paving way for increased turbine availability.
Major defect discovery in the beginning also provides the chance for cost savings as the extent of repair is lesser, curtailing the related costs for access to the rotor blade, and potentially thwarting tragic malfunction of the rotor blade.