New design for offshore wind substations in the wings
WindEnergyUpdate speaks to David McVeigh, Harland & Wolff, about its latest design for the Gwynt y Môr offshore substations and an R&D programme that aims to resolve several offshore transformer platform challenges.
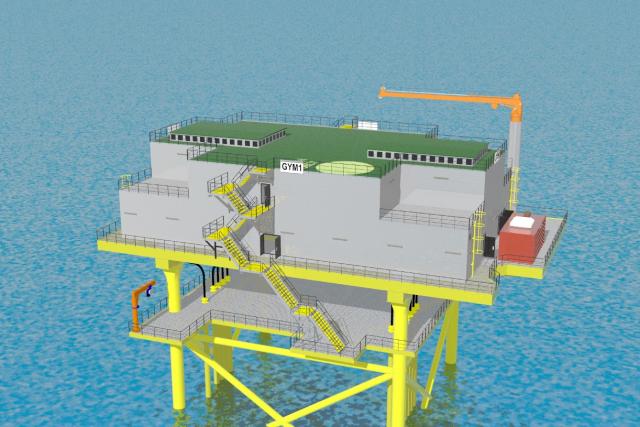
By Rikki Stancich in Paris
The contract recently won from engineering conglomerate Siemens, for the design and build of two offshore substation platforms for the Gwynt y Môr offshore wind farm off the coast of North Wales, represents more than just a toe dip into the offshore wind industry for Harland and Wolff Heavy Industries Limited.
Following a massive investment into new manufacturing kit in order to gear up for the pending boom in offshore wind projects, Harland & Wolff is now open for business.
The Siemens contract will see Harland & Wolff deliver two innovative substations for the 576MW, 160 turbine Gwynt y Môr offshore wind farm, which is a UK Round 2 wind farm being developed by a consortium of RWE Innogy, SWM – Municipal Utility Munich, Germany and Siemens 13km off the coast of North Wales. The substations will be completed by June 2012.
The platforms have been designed using stiffened panels typical of shipbuilding and offshore structures. According to Harland & Wolff, this approach offers cost and weight savings, increased watertight integrity, structural flexibility and opens opportunities for floating, self-installing projects in the future.
WindEnergyUpdate’s Rikki Stancich speaks to Harland & Wolff Sales and Marketing manager, David McVeigh, to learn more about the Siemens contract and about H&W’s forward strategy for the offshore wind energy sector.
WindEnergyUpdate: What new technologies will be used for the Gwynt y Môr offshore substations?
David McVeigh: The substations will utilize the latest Siemens transformers. From a construction point of view, the substation structure will be a stressed skin design more typical of a watertight marine structure or vessel, rather than clad beam and column structure.
We believe this is lighter, stronger, and more durable in this particular case. This design is also more adaptable throughout the life of the structure as you have a stiffened steel structure from which fit new pipe or cable runs.
WindEnergyUpdate: What challenges are presented by the design and build of substations for the offshore wind sector?
David McVeigh: Harland and Wolff have a lot of experience in the offshore oil and gas sector but until recently, our manufacturing equipment was designed to cater to a similar, but not the same, industry.
A huge investment in new plant and equipment that is particularly suited to the offshore wind industry, has dramatically reduced costs, allowing us to offer market leading quality and pricing for substation platforms and jackets for turbines and substations.
For example, using the appropriate tools for the job has enabled us to reduce the welding man-hours to one-third of what they were.
WindEnergyUpdate: To what extent has the equipment investment placed Harland & Wolff ahead of its competitors?
David McVeigh: Our advantages are not only in the revitalized plant and equipment, but with our in-house design team and skilled and committed workforce. For example, we produce bespoke offshore modules for the same price, and in the same timeframe, as modular units offered by some competitors.
Proof of this is the recent conversion of a semi-submersible drilling platform. Harland and Wolff were contracted to design and build a 130 man accommodation module and large power generation module, essentially a containerized hotel and power station. From a written specification and blank footprint, these were designed, built, out-fitted and delivered in ten months.
WindEnergyUpdate: How have you addressed O&M and safety issues with the built design?
David McVeigh: Safety is of paramount importance to Harland and Wolff and to our customer Siemens.
The design of the module is to the very latest DNV and UK HSE standards, as you would expect. Coming from the offshore oil and gas sector, this is standard practice for us.
We are working closely with the operator to ensure O&M input is incorporated at the earliest stage possible in the design process.
WindEnergyUpdate: Harland and Wolff has been working on an R&D programme aimed at developing solutions to key issues that exist in the offshore wind industry. Can you provide an overview of the R&D programme?
David McVeigh: For the last eight months we have been speaking with most of the Round 3 developers, O&M contractors, installation contractors and offshore wind farm operators in order to gain an understanding of the problems they experienced with substations and to develop a best-in-class solution that addresses these problems.
Based on this research we have designed a transformer platform that addresses a considerable number of the issues experienced at either installation or during day-to-day operations.
The driver for this is not simply to be concerned with reducing manufacturing costs alone, but thinking about the whole substation life cycle costs; a good design need not be more expensive to build if considered early enough.
Examples of some of the issues discussed and improved include cable installation on the cable deck, mechanical handling and maintainability.
WindEnergyUpdate: How is Harland and Wolff positioned to service the pending demand spike from the UK offshore wind sector?
David McVeigh: We all understand the large number of offshore wind farms to be developed in order to meet the Government’s targets.
Manufacturing in Western Europe is generally excellent; Harland and Wolff have the additional advantages of vast capacity and physical scale.
With our existing facilities we are capable of producing a great number of jackets and substations every year. Almost uniquely, with the large amount of hard starting ground adjacent to our docks and quaysides, we can build and hold the jackets and just-in-time deliver them in line with our customers’ requirements.
To respond to this article, please write to the Editor: Rikki Stancich
Image: Gwynt y Môr substation designed by Harland & Wolff. Image courtesy of H&W.