Innovative foundations could make specialist installation vessels redundant
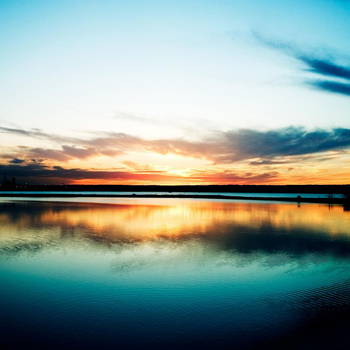
Xanthus Energy has designed what it describes as a self-installing gravity base, removing the need for specialist offshore plant and vessels. WindEnergyUpdate talks to Xanthus Energy CEO, Lewis Lack, to find out more.
By Rikki Stancich in Paris
A consortium between Xanthus Energy Ltd, Able UK Ltd, a land-owner and port operator, and engineering firm Ekspan Ltd, was recently awarded a grant by UK’s Northern Wind Innovation Programme (NWIP) for the development of a new self-installing gravity base that promises to reduce installation costs and timescales and remove the need for specialist plant and vessels offshore.
The consortium has devised what it says is a viable plan for quayside manufacturing and construction of the self-installing turbine foundations, with the assembled foundation structures and turbine components then floated out to site using a standard barge.
WindEnergyUpdate: Can you describe how the SeaBreeze ‘self-installing gravity base’ works?
Lewis Lack: The idea is to try and simplify the concept, reduce the risks and the costs and to accelerate the process of installing offshore wind turbines.
The SeaBreeze foundation uses the principal of buoyancy, allowing the fully assembled wind turbine, to be floated out, ballasted and installed onto the seabed.
We are moving the focus away from specialist vessels, which are capital intensive to build and have a high day rate. Our concept, on the other hand, requires only a basic tug, rather than a specialist vessel.
WindEnergyUpdate: What issues does the proposed self-installing gravity base solution resolve?
Lewis Lack: We are proposing a step change, insofar as currently, specialist vessels can take out 5-6 turbines and foundations components. Those specialist construction ships then need to go out and sit out there while assembling the turbines. Using this method in Round 2, it took typically up to two years to install a complete wind farm.
We on the other hand, propose to take the fully assembled turbines out using standard tugs. This system is much more flexible than current systems.
For example, a wind turbine mounted on a SeaBreeze foundation could be installed in 2.5m seas and towed safely in 8 metre seas if the weather changed during tow out, where the current standard is one metre seas.
In this sense, we could significantly narrow down the weather window. Once on site offshore, in the ballast could be achieved in a maximum of 6 hours and then you can get back to shore. . You can tow more than one at a time – you could have a train of, say, three going out at any one time.
We think that with our system, you could have 50 wind turbines installed and grid-connected with six months.
WindEnergyUpdate: What are the downsides?
Lewis Lack: Certain seabed conditions exist where this technology may not work.
They are big structures, so you would require a significant amount of land space to build an onshore foundation and assembly factory. That said, they may be big on land, but the size is nothing compared to the size of the proposed offshore wind farms and the ocean where they will sit.
These foundations can be installed in up to 60 metre water depths, which covers all of the Round 3 projects.
Beyond 60 metres, floating technology is more viable. Our floating wind turbine technology has already been proven with the buoy structures, but they too, need to go to full-scale demonstration. These floating foundations are more suited to far shore locations or where deeper waters exist such as the Mediterranean Islands, or off the coast of Portugal.
Compare the 7000 tonne structure of the Hywind project to our proposed 700 tonne OceanBreeze structure and the cost advantages are obvious. However, we have yet to prove it.
WindEnergyUpdate: What scale of quayside facility is required?
Lewis Lack: The foundation factory rate of delivery required for Round 3 is approximately 200 units per year, per wind farm. The turbines would be largely commissioned onshore, whereas previously, turbine assembly has occurred offshore. It makes more sense, given that it is easier and much cheaper to remedy early problems when the structure is adjacent to the quayside.
You would need a concrete batching plant, large cranes to assemble the turbines, electrical connection to the electricity grid for compatibility checks. A major plant would be turning out more than 2-3 structures per week per production line.
We are working with our partners, who have ports that could accommodate these kinds of factories. Able UK, who is one of our partners, has Able Seaton Port (ASP) and Able Humber Ports (AHP) facilities both of which could handle the required factory and supply chain.
We are currently modeling and testing the concept to calibrate our analytical work, in order to prove the viability of the project prior to going to a full-scale demonstrator.
WindEnergyUpdate: What are the projected costs?
Lewis Lack: We have put a lot of energy into developing a detailed planning and costing of the supply chain requirement. Our expectation is to reduce costs to below the targets set by the Carbon Trust OWA programme.
WindEnergyUpdate: Have you completed any pilot schemes and if so, what were the results?
Lewis Lack: The technology has already been used elsewhere. It uses both the principals of a buoyant structure and a gravity base, both of which have already been used on our sister company’s oil and gas products as a low cost option for accessing reserves in marginal fields.
To date we haven’t actually floated a turbine out on one of them. We are currently in discussions to secure the funding for a full-scale prototype. The idea has been developed off the back of Ocean Resource’s platform and buoy systems
Xanthus was set up to take the concepts and patents filed a few years ago by Ocean Resource and apply them to the wind energy sector.
WindEnergyUpdate: What are the environmental advantages of SeaBreeze foundations compared to existing foundation models?
Lewis Lack: Our foundations can be installed with little disturbance to the seabed or the mammals that live in the sea (such as dolphins) unlike piling which is noisy.
We do not need to dig up and prepare the seabed either, unlike some other concrete gravity base suppliers. In addition, since we are using small vessels for short sorties to the offshore wind farm, the CO2 output from these vessels is much smaller than the large specialist supply ships that sit offshore for months during a wind farm construction.
And while the manufacturing of cement produces CO2, concrete does continue to absorb CO2 during its lifetime. The foundations also provide an attractive location for fisheries to develop.
WindEnergyUpdate: How has the idea been received by the industry?
Lewis Lack: There has been a lot of interest. We have been engaging with the industry for over 2 years and several developers have already requested information for inclusion in their environmental impact assessments. I think once we have a full-scale demonstrator model in the water, we will generate a lot more interest.
We have also spoken to wind turbine manufacturers, as there is a need to connect with them regarding the engineering process. You can’t design a foundation without considering the tower, wind turbine and the installation process. For example, bracing may be required for transporting the turbine to site. We have had a more cautious reception from the manufacturers.
WindEnergyUpdate: Aside from the funding awarded by NWIP, has the project received any other funding?
Lewis Lack: NWIP is the sole source of funding to date. The concept was short-listed for the Carbon Trust’s Offshore Accelerator (OWA) program fund, but we didn’t make it through to the final round. I think we missed out on that more due to a lack of understanding.
WindEnergyUpdate: In your view, how could the UK government better support offshore wind?
Lewis Lack: The government is now moving in the right direction. The recent series of meetings held by the Crown Estate have been useful. Finance is still needed to develop the supply chain and Central Government could certainly help with that. Engineering firms continue to have difficulties raising capital for plant investments.
The Crown Estate’s plan to give licence extensions to Round 2 is about providing the supply chain opportunity to develop before Round 3 supply gets going. But the fact is, huge hurdles still exist.
For five years we have been sitting and thinking and planning. Suppliers want to gear up, but we need the business to be there in the first place. We need faster approval of sites and permitting in order to give business a chance to ramp up for Round 3. The key concern is: How will suppliers suddenly ramp up from zero to 200 units annual supply overnight? Clearly, the sooner we get going, the better.
The licences and approval process needs to be accelerated. The IPC should help in this respect, but they need to get their act together and get a move on. If they could lop a year of the process, that would be very useful.
To respond to this article, please write to the editor:
Rikki Stancich: rstancich@gmail.com