How Belwind is beating the odds
The proposed 330MW Belwind project took a major hit during the onset of the economic downturn. Wind Energy Update speaks to Belwind project director and managing director of Belwind NV, Frank Coenen, to find out how the project recovered to emerge stronger than ever.
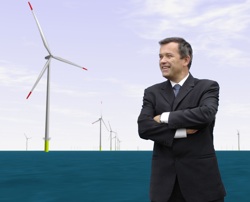
By Rikki Stancich
Despite a major knock during the project’s early stages, Phase 1 of Belwind NV’s 330MW offshore ‘Belwind’ wind farm has already set several records, and the project looks in good shape to come online before 2011.
Not only is Belwind one of the fastest offshore wind farms to have been constructed to date (taking a total of 3.5 years from concept to construction); it is the first and largest offshore wind farm to have been financed on a non-recourse basis since the onset of the financial crisis.
Belwind’s project leader Frank Coenen demonstrated remarkable sangfroid when Belwind’s majority shareholder Econcern went bankrupt only months prior to the project’s financial close date. In the throes of the financial crisis, Coenen managed to bring together a consortium of Belgian and Dutch investors, including PMV, Meewind and Rabo Project Equity, in order to raise €620 million for the first phase of the project.
The project’s financiers include a consortium of Banks, managed by Dexia (senior) and Rabo Bank (mezzanine), the European Investment Bank, EKF (Denmark’s Export Credit Fund), Dutch investment bank ASN, Dexia, and Rabo Bank.
Located near Bligh Bank, some 46km off the Belgian coast in water depths of up to 37 metres, Belwind is currently the farthest from shore wind farm in the world. Creative thinking on the part of the project engineering team enabled the project to be realized in a cost-effective, timely manner, with the first monopile installed within 2 months of financial close.
Admittedly, even as Phase 1 of the 330MW project nears completion, Belwind is being overshadowed by Forewind’s vast Round 3 Dogger Bank project, which is to be located some 290 km from shore at its furthest point, in water depths up to 63 metres.
But for now, Belwind has demonstrated - against the odds – that far shore turbine installation is both financially and technically feasible.
In the first of a two part series focusing on the Belwind project, Wind Energy Update speaks to Frank Coenen to learn more about the challenges presented by far-shore wind farms and the installation tactics that can be deployed to enable a swift – and cost competitive – build out.
Wind Energy Update: From an installation perspective, can you describe the challenges that you were up against with the Belwind Bligh Bank project?
Frank Coenen: In terms of technical challenges, at between 46-51 kilometers from the shore, in water depths of between 20-37 metres, Belwind is currently the furthest wind farm from shore in the deepest waters.
Wind Energy Update: What logistical challenge did this present and what creative solutions were developed to resolve this?
Frank Coenen: In terms of the logistical chain, this project was special in that 50km had to be covered with very heavy equipment. The monopiles each weighed between 400-550 tonnes and somehow had to be transported to Bligh Bank.
One option was to load them onto a barge - which would have involved transporting and lifting the 70m long, 6m diameter structures horizontally so as not to capsize the vessel during installation.
Instead, our engineers came up with a solution that involved plugging the ends of the monopiles and floating them, in order to tow them to site using a standard tugboat. Once the monopiles were towed to site, we used a crane to lift one end, while the other plug was depressurized, so that the monopile could be vertically lowered into position and hammered into the seabed.
This solution delivered considerable cost savings with regard to time, vessel and crane costs.
Wind Energy Update: Can you describe the installation strategy for the turbines?
Frank Coenen: In addition to the monopiles, the transition pieces, cables and turbines were pre-assembled in the harbour and brought to the sand bank. This involved huge pre-assembly activity at the harbour.
Vestas managed to carry out a complete hot-commissioning, which means the towers and nacelles were assembled in the harbour, linked to a land grid and fully tested (energised) before being transported out to the wind farm site.
We managed to install one turbine every 6-7 hours – it was a fantastic job. The turbines were installed as plug and play, given that the offshore substation was energized, so effectively the turbines could be switched on as soon as they were installed.
Wind Energy Update: How would you rate the foundation and turbine installation vessel performance? Would you use these vessels again?
Frank Coenen: We used the vessel Svaenen for the monopile installation and the jack-up barge (JB) 114 for installation of the transition pieces. When you hammer in gigantic monopiles that are 70m long, it is quite normal that the piles are not entirely straight – they may lean slightly to the left or right. The transition piece compensates for this.
We used the Sovereign vessel for burying the infield cables linking the turbines to the offshore substation.
Nexan’s Skagerrak was – and still is - responsible for laying the export cable, while the HAM 601 also installed the inter-array cables and lay down the scour protection (the bed of stones and rock installed on the sea bed to prevent erosion around the foundation).
All of these vessels performed well.
Wind Energy Update: Why were the Vestas V90 turbines deemed most suited for this project?
Frank Coenen: Technically, the choice of turbine was very important. We went with the Vestas V90 for one main reason: it is light and suitable to build on monopile turbines – it enabled us to avoid using concrete gravity base and jacket foundations.
Wind Energy Update: The Belwind project is described as the fastest offshore wind development in the world, which is no small feat considering the project’s former majority shareholder went bankrupt. How did you manage to keep the project on track?
Frank Coenen: The project reached financial close on the 24th July 2009. On September 08, 2009, the first monopile for Belwind was installed. By the end of November 2010, all going to plan, Belwind should be online.
The pilot for the Belwind project was carried out in 2008, which is when we arranged the financing. By the end of 2008, the financial crisis was in full swing and then in March 2009, the project’s main sponsor, Econcern, went bankrupt.
So we had the projects contracts and the banks ready, but we had no shareholders. Trying to find €620 million in the middle of an economic crisis was pretty tough.
I think the fact that the EU committed to its 2020 Renewable Energy targets and that we had managed to get the pilot completed in the middle of an economic crisis put us in good stead.
A major strength of this project is that the people involved are very ‘down to earth’, in that we focused on bringing a lot of existing know-how. We were never too proud to hire the right people with the right experience, and the project was very much run on a ‘best practice from lessons learned’ basis.
There are a lot of engineering firms in this sector trying to develop solutions from scratch, without making use of existing know how in the market. Even the contractors tend to use new people on the job, instead of building on acquired know-how.
Belwind has been very efficient at searching for and finding the right know-how. We have used a lot of people that have come from an oil and gas background, but who also have a lot of previous experience in the offshore wind sector. There is a huge difference between offshore oil & gas, and offshore wind.
Wind Energy Update: Looking into the future, as the owner-operator what is Belwind’s turbine O&M strategy, during and post warranty phase?
Frank Coenen: Turbine access from boat to turbine is always complicated and there are safety issues if the swell is high. This means that maintenance needs to be scheduled for good weather days.
The choice of vessel is important. Our contractor, Vestas, who carries out the maintenance, has opted for a hotel ship, which will remain at the wind farm site. The O&M crew will stay and live on the hotel ship to be transferred directly to the turbine, so this cuts out the 50km transfer from shore to turbine
After five years we will look into the option of carrying out O&M in-house or continuing with Vestas. So far, we are very happy with Vestas.
To respond to this article, please write to the editor: Rikki Stancich