Drive train reliability: overcoming traditional problems, unearthing new breakthroughs
Overcoming problems associated with Drive train reliability is one of the key issues now within the wind energy sector. All drive train concepts are based on two major factors: cost and risk. Wind Energy Update explores the latest developments in this...
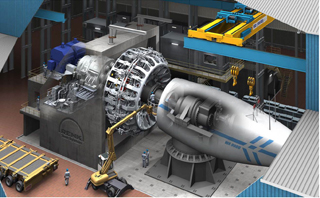
By Ritesh Gupta
Drive train dominates the performance of the wind turbine after the rotor. It involves the main technical performance issues, efficiency and is one of the most important contributors to the wind turbine costs together with the blades and the tower. The focus of the industry towards better, more efficient, reliable and cost competitive drive train concepts is an ongoing research arena in which the industry continues to debate and invest.
The industry has improved upon reliability of drive trains in two main areas. The first one is related with the design process and the understanding of the behaviour of the drive train in terms of dynamics and loads. This has been done improving design methodologies, simulation tools and improvement of the correlation between experimental and numerical data. The second one is related to the engineering and manufacturing process, involving a clear focus and effort towards the improvement of the quality of the components and its test and verification before shipment.
Breakthrough concepts?
One of the main problems of conventional drive train concepts is that the components are performing structural and mechanical functions at the same time, which makes it challenging to simulate loads properly at the design stage. This is especially critical in components as complex as a gearbox and direct drive generators, which are basically designed to withstand torque moments.
Alstom considers its Pure Torque drive train design as the most efficient way to solve this problem because it uses a rotor support concept that separates structural behaviour from mechanical behaviour, according to Jordi Puigcorbe, Alstom vice president for innovation in wind business.
“This concept is a breakthrough in drive train technology because it is used successfully in onshore and offshore wind turbines independently of the use of geared or direct drive generators. The separation of torque moments and bending moments coming from the rotor increases drive train reliability independently of the configuration, i.e. geared or direct drive,” says Puigcorbe.
Drive train reliability is one of the key issues now within the wind energy sector, but physics and stressors of failure modes are challenging, says Dr. Andrei Mander, operations director of the Wind Turbine Drive Train Testing Facility at the Clemson University Restoration Institute in North Charleston, South Carolina.
“These require new approaches in testing and product validation resulting in creation of advanced test centres, with advanced testing capabilities and validation methodologies,” says Dr. Mander.
Development
Dr. Mander points out that all concepts are driven by two major factors: cost and risk. Under current wind market development, he expects major players to remain on their current concepts – there are no resources for wide research, and higher risks cannot be taken, he says.
“Direct-drive development will be limited by permanent magnet[s] cost; the geared solutions remain solid, helped by strong increases in reliability increases in recent years. The mid-speed solution has potential for mass–size optimisation for turbines in the 5 MW-plus range,” says Dr. Mander.
Alstom’s approach is always based in a total cost of energy analysis and optimisation. This exercise is performed considering all affecting parameters in onshore and offshore conditions. Alstom has in its portfolio DFIG (doubly fed induction generator) and direct drive solutions for onshore and offshore, respectively, demonstrating that the best technical solution is dependent on the kind of application and boundary conditions in which the wind turbine has to operate.
Puigcorbe says the progress has been huge over the years, clearly indicating the importance in terms of cost and performance of the drive train in the wind turbine.
He further adds that the most accepted drive train concepts in the industry today are very similar to the ones identified 10 years ago, i.e. doubly fed induction generator, direct drive and geared mid speed.
According to Puigcorbe, differentiating onshore DFIG and full power concepts has been an active area of discussion in which the DFIG solution has demonstrated superior cost competitiveness fulfilling all performance requests. In offshore, the debate is still under analysis and two concepts are clearly competing, i.e. mid speed gear versus direct drive.
“Even some public analysis suggests that the differences between both concepts are small; a total cost of energy analysis considering offshore costs breakdown and boundary conditions positions direct drive solutions as the most competitive concept for the offshore industry,” says Puigcorbe.
Winning Concept
For onshore, the analysis clearly shows that DFIG is the most competitive technology up until the range of 3MW, says Puigcorbe. Efficiency and cost of components are the main drivers in that particular case.
For offshore, the solution indicates that direct drive is the best solution for wind turbines in the range of 6MW, being reliability and maintenance cost being the key drivers, according to Puigcorbe. Other alternatives to these two technologies have been discarded due to its poor competitiveness and performance, he adds.
Cost Reduction
According to Alstom, a good correlation and link between experimental behaviour and design models allows improvement of materials and component optimisation impacting clearly on the cost of the drive train. This includes mechanical optimization, weight reduction and reliability improvement reducing O&M costs.
In addition, Alstom is extremely focused on the standarisation of main components to reduce costs using volume effects. Clearly, this standarisation requires to be incorporated in the early stages of the design process, says Puigcorbe.
The industry is moving in the right direction, but the desired results are not yet here. According to Dr. Mander, to get the right reliability figures from the field for new platforms in the 5MW-plus range, the industry needs at least 5 to 10 years of operational experience. Reliability testing at test centres is one way to deliver proven reliability results.