Direct drive turbines: Lean, mean, but not so green
Direct drive is becoming the technology du jour for large offshore wind turbines. But is it wise to trust an unproven design that relies on highly polluting, scarce materials?
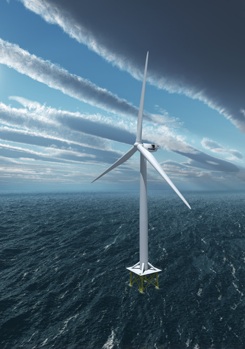
By Jason Deign in Barcelona
Siemens’ SWT-6.0-120 6 MW offshore turbine will be a direct-drive machine. GE’s 4.1-113 4 MW offshore turbine will be a direct-drive machine. Alstom’s forthcoming 6MW offshore turbine will be a direct-drive machine. Vestas’ V164 7.0 MW offshore turbine will be… oh, wait a second.
The news earlier this year that Vestas would not be using direct drive for its new flagship offshore machine caught many in the industry off guard.
“The majority of new manufacturers are opting for direct drive,” says Eduard Sala de Vedruna, research director of Europe Wind Energy Advisory at IHS Emerging Energy Research. “The announcement by Vestas was unexpected. The fact it chose a hybrid was a surprise.”
Is it a wise move, though? There is a good reason why offshore turbine manufacturers are planning or building direct-drive machines. Because the rotor is linked directly to the turbine blades with no need for a gearbox in between, there are far fewer moving parts.
According to Birger Madsen, head of Navigant Consulting’s BTM Consult division: “Siemens say they have reduced the number of parts in the nacelle to half of what it was. Fewer parts, means fewer problems.”
In an offshore environment, where the simplest of maintenance tasks can cost tens of thousands of dollars, this potential improvement in reliability is a big selling point for direct drive.
Risk takers
Madsen believes offshore sales will drive direct drive’s share of the turbine market up to 25% in the next few years, a significant increase on the 17.9% level that onshore makers such as Enercon and Goldwind held in 2010. But the move to direct drive is not without its risks.
Principal among these is the fact that nothing like this has been tested previously in an offshore setting.
Enercon, whose tried-and-tested direct-drive turbines commanded 8% of the total wind market by energy capacity in 2010, according to BTM Consult, uses a separately excited annular generator too heavy for use at sea. The company has not announced an offshore machine.
As a result, operators buying into direct drive may expect fewer maintenance problems. But they are also relying on an untested technology and face the prospect of not knowing what is likely go wrong, or how difficult and costly it will be to fix.
Furthermore, to get around the weight challenges posed by the excited annular generator design, Siemens and others are adopting an alternative direct drive arrangement using permanent magnets made up of the rare earth metal neodymium.
When Siemens first achieved this it was considered something of a breakthrough, says Madsen. “My feeling about direct drive was that it was heavier and it was more expensive. That was a concern.
“But when Siemens launched their 3 MW machine one and a half years ago, the weight was a little bit lower than their 2.3 MW machine. It was surprising for me that they had succeeded in making such a light machine.”
Since then, Siemens has led the way in direct drive technology based on permanent magnets. Its SWT-6.0-120 6 MW offshore model, unveiled this month, “is the third machine in our direct-drive family,” states company spokesperson Eva-Maria Baumann.
However, more than 90% of the world supply of the rare earth metals the design relies on is currently controlled by China, which has restricted exports in the past. This has led some to fear that growing demand from the offshore wind industry could lead to a bottleneck.
Madsen believes this is unlikely given existing deposits in Australia, the USA and elsewhere. But a seperate factor working against the rare earth material, is that neodymium mining is highly polluting – a factor that tarnishes wind energy’s green credentials.
Hedging their bets
Against this backdrop, Vestas’ decision to face off Siemens with a hybrid design seems to have some merit, giving investors a tried-and-tested alternative to direct drive.
To counter concerns about reliability, the V164-7.0 MW is equipped with sophisticated control and failsafe systems that should reduce the need for unscheduled maintenance.
What still is not clear, though, is “did they announce this strategy due to a lack of knowledge and ability [to produce direct-drive turbines], or because they believe in it?” Madsen says. All of which is likely to leave operators scratching their heads over which option to choose.
Dong Energy, the world’s biggest offshore wind developer, is reported to be evaluating the new turbines from both Siemens and Vestas.
But since the cost benefits for direct drive versus gearboxes are only expected to become apparent over the lifetime of the machines, it could take a while for meaningful results to emerge.
Sala de Vedruna at Emerging Energy Research says: “These are just concepts at the moment. Right now the numbers around them are pretty much unknown. These turbines are being produced for a market that has not been tested yet. Only time will tell whether they work.”
Image credit: Vestas' V164-7.0 MW hybrid offshore turbine
To respond to this article, please write to:
Jason Deign: mail@jasondeign.com
Or write to the editor:
Rikki Stancich: rstancich@gmail.com