Direct drive: A step change in turbine design?
A host of manufacturers are developing direct-drive turbines for offshore use. Where does this leave the gearbox?
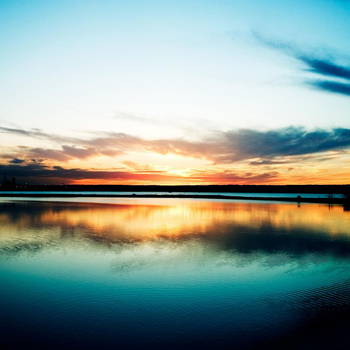
By Sam Phipps in Edinburgh
When the likes of General Electric and Siemens are on to something, competitors usually take note.
Both companies, giants in the renewables industry, are investing seriously in direct drive generators for offshore wind farms, replacing the more widespread gearbox technology.
It raises the question of whether direct drive is superior or just different, and whether other manufacturers will follow suit.
Carlos Haertel, managing director of GE Global Research, is in no doubt about the systems’ relative merits.
“We will continue with gearboxes for our 1.5MW and 2.5MW [onshore] systems,” Haertel has said. “But for offshore turbines a gearbox is not a good idea… there will not be further development of gearbox systems for offshore.”
Direct drive eliminates the need for a gearbox by means of a permanent magnet attached to the rotor, which connects to a generator. It means fewer moving parts, thereby potentially improving reliability and cutting operation and maintenance costs – areas that are often cited as liabilities in the offshore wind sector.
With major expansion due in Europe alone in the next few years – offshore wind is likely to account for a large part of the 20% of energy that must come from renewables by 2020 – the choice of direct drive or gearbox will potentially be crucial.
Henrik Stiesdal, CTO of the Siemens Wind Power Business Unit, says its new SWT-3.0-101 will offer 25% more power than the present 2.3MW turbine, but with a lower weight and only half the parts. Commercial serial production is expected to start in 2011.
“Our main target for the new machine was to reduce complexity in order to increase reliability and profitability. We are confident that our new direct drive wind turbine is a reliable investment in the future of power generation,” he says.
At 6.8m long and a 4.2m in diameter, the nacelle can be transported using standard vehicles commonly available in most major markets, Stiesdal says. “But despite the compact design, we have actually given our service technicians more space to operate – simply because we radically reduced the number of parts”.
The new turbine uses a synchronous generator that is excited by permanent magnets. These convert the rotor movements directly into electrical energy. The new generators in the gearless test machines are among the largest permanent-magnet machines ever built, running with torques of about 2,500 kilonewton meters. By comparison, a powerful car’s engine has a torque of less than one kilonewton meter.
General Electric, meanwhile, is planning to build the UK’s first wind turbine manufacturing plant for equipment to be used in the UK (the Vestas factory that closed in 2009 on the Isle of Wight made onshore turbines for the US market). The site, yet to be disclosed, will produce 4MW turbines exploiting the direct drive expertise that was acquired from ScanWind, which GE bought last year
Another major player in direct drive is XEMC Darwind, formed last year when Chinese conglomerate XEMC took over the Dutch startup. Darwind's DD115, a 5MW turbine, is due to be trialed in one-year tests in both the Netherlands and the UK later this year.
Larry de Vaal, business development manager, said: "We expect gear-type offshore turbines will be phased out soon after the direct drive models have built up a convincing track record, three to five years from now."
"Our new mother [XEMC] is very ambitious to become a global player and to start manufacturing these turbines in China," says Darwind chief executive Vincent van den Brekel. "The ramp-up [in Europe] could be very swift indeed."
Price competitive?
However, despite these developments, the days of the gearbox are far from numbered. Michael Holm, director of group communications at Vestas, the world’s largest turbine manufacturer, with a global market share of around 28%, says: “Our whole product line has a gearbox as it’s the most economical technology and brings the most return. Even if you have to replace the gearbox over the life of the turbine, it is cheaper than direct drive.
“We are not commenting on what’s in our R&D pipeline but you can draw your own conclusions on strategy from our latest turbine, the V112.”
The new 3MW Vestas flagship is geared, providing what the company says is “exceptional rotor-to-generator ratio for greater efficiency”, and delivers “high reliability, serviceability and availability under all wind and weather conditions.”
The V112 is said to start operating at wind speeds of only 3 metres per sec, compared with the more common 5 or 6 metres per second of other turbines in its class.
“For customers, it’s not a question of either direct drive or gearbox – it’s about the cost of energy, how you make the most efficient system,” Holm says. By the same token the company has found 3MW is the optimal maximum for turbines. It could make larger ones but they would be too costly to bring value, he says.
Permanent magnets also require rare earth metals, most of which are sourced in China, and concerns over availability of supply are growing.
Direct drive might be making inroads then, but the turbine gearbox has plenty of life in it yet.
To respond to this article, please write to:
Sam Phipps: samcphipps@yahoo.co.uk
Or write to the editor:
Rikki Stancich: rstancich@gmail.com