Balancing risk and opportunity: The challenge of designing a better offshore wind turbine
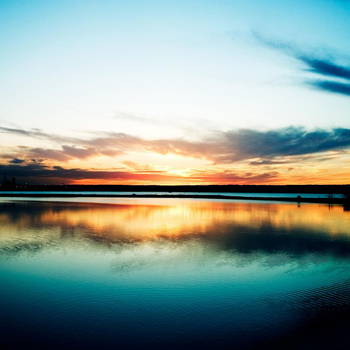
A step change in design is needed if offshore wind turbines are to become cheaper and more reliable
By Zara Maung
The offshore wind industry has come a long way since the first wind turbines were set up off the coast of Denmark in the1990s, but manufacturers have had their fingers burnt on the journey. The first generation of offshore wind turbines were essentially onshore turbines stuck out in the sea. Inevitably, they fell victim to corrosion from the sea. Gearbox failure also became a problem as the turbines were damaged by salty conditions and stronger, less predictable offshore winds. Manufacturers had to pay out millions of euros as a result. This was epitomised by the disaster at the Danish Horns Rev offshore wind farm in 2005, where Vestas had to remove and repair 80 of its V90 models after only two years.
Offshore turbine manufacturers now tailor their turbines to offshore conditions, using anti corrosion paints borrowed from the oil industry, bigger turbines to harness the forceful offshore wind conditions and better pitch optimisation (blade positioning) to avoid gearbox damage.
But work still has to be done to make offshore wind energy cost competitive to fossil fuel power, a goal taken on by the UK’s Energy Technologies Institute, a government supported funding body for renewable energy innovation. Although manufacturers say that offshore turbine availability (the percentage of time the turbine is available to turn) is 98%, equal to that of onshore turbines, in reality offshore wind turbines are out of operation far more than their onshore counterparts due to lengthy scheduled maintenance periods. These downtime periods in turn make a big dent in the side of offshore wind farm profits.
Direct drive – The future for offshore wind?
A major stride towards getting offshore wind turbines up and running more of the time would be to take the gearbox out of the turbine altogether, and replace it with a gearless direct drive system, says offshore wind expert Charlie Hodges of New Energy Finance. Cutting out the gearbox will avoid the need for a twice a year service and gearbox replacement every 10 years. Affordable direct drive turbines are still 3-5 years away however, says Hodges. Big manufacturers are starting to buy up the technologies needed to develop direct drive, GE’s purchase of ScanWind this month being the latest example. Hodges believes that offshore manufacturer, Darwind, which recently went into liquidation, will also be snapped up soon for its direct drive technology.
LIDAR – Lighting the way ahead
Further technological innovation to improve offshore wind turbines includes the use of LIDAR (Light Detection And Ranging) technology. This is essentially a wind tracking radar that can help to predict the strength and direction of gusts before they hit the turbine. It would allow the turbine to readjust to make optimum use of the wind conditions and to manage loads on the turbine and prevent wind damage. Soren Houmoller, Director of offshore technology at Vestas Offshore, says that Vestas is working on fixing LIDAR technology to its turbines, although improvements still need to be made to improve the reliability of the wind data collected and the turbine’s corresponding attempts to achieve pitch optimisation.
Bad vibrations
Tower dampers are another feature likely to become a standard in offshore wind towers according to ? from DONG Energy, as they prevent vibrations from the waves at the base of the tower from interfering with the turbine.
Fewer vibrations and less load on the turbines will mean manufacturers can build lighter and cheaper wind turbines, with scaled down wind tower foundations. Further challenges will be added as wind farms start to enter deeper waters of 30 to 60 meters, says UK Carbon Trust’s Ben Sykes, head of the offshore wind accelerator programme at the UK’s Carbon Trust, a government owned company. Deepwater wind farms are being considered as part of the UK’s offshore wind development programme’s round three, launched last year. Developers will need more reliable turbines and new innovations in wind turbine foundations to be able to keep the costs of deepwater wind farms from spiralling, according to Sykes.
Offshore turbine manufacturing remains a risky market, however, hindered by the large payouts for faulty equipment and regulatory uncertainty over UK offshore wind installation. A limited number of manufacturers, namely Vestas, Siemens and RE Power, dominate offshore turbine sales at present, which has inevitably limited design innovation.
Sykes, who is working with the ETI to help develop low cost, high power offshore wind farms, expects new competitors to enter the market as offshore wind development accelerates. US turbine manufacturer Clipper Windpower is one contender. Clipper has already secured a pledge by the UK Crown Estate, coordinator of UK offshore development, to purchase the company’s 10MW turbine, which is still in early R&D stages. “There’ll be 4-7,000 wind turbines offshore by 2020 so we’ll see significant market growth” says Sykes. However, while regulatory reform in countries such as the UK has increased demand for turbines almost overnight, technological improvements are far more gradual, says Hodges. Offshore turbines are still very much “work in progress” but crucially these developments should lower the overall cost of offshore energy.