Handling lubrication-related issues with precision
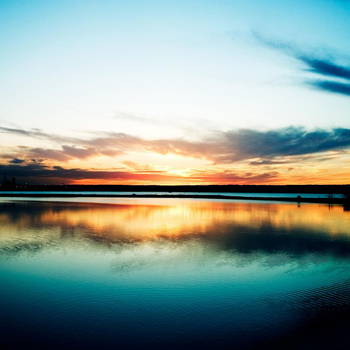
Wind turbine manufacturers – along with their component suppliers – have been “raising the bar” for lubricant’s performance.
Many field-operating failures are a consequence of gearbox bearing failure. This type of failure is believed to be directly related to poor lubrication and lack of routine maintenance.
Referring to Sandia National Laboratories’ study on wind turbine reliability, ExxonMobil Lubricants & Specialties’ Global Mobil SHC Technical Advisor, Kevin Harrington, says gearbox failure was identified as a major contributor to wind turbine downtime and in particular, bearing failure was cited as a major cause of these failures.
However, inadequate lubrication was not identified as a contributor to these bearing failures, added Harrington.
High performance wind turbine gear oils can contribute to increased wind turbine availability through longer oil drain intervals – reducing downtime to change oil, extended filter change intervals – reducing planned and unplanned downtime for filter changes, and extended gear box life – postponing gearbox removal and replacement and reducing downtime for gearbox replacement over the life of the turbine.
The critical lubrication requirements include first, the main gearbox; second, large bearings on the main shaft, the pitch bearings on the turbine blades and the yaw bearings at the base of the nacelle; and third, the high speed bearings on the generator.
In addition, proper lubrication is required in gear motors used in the yaw drive and pitch control systems. Finally, high performance hydraulic oil should be used in the emergency braking system and in the hydraulic pitch control systems, which are used in some wind turbines, according to Harrington.
Trends
Harrington refers to two important trends in this area.
First, wind turbine manufacturers – along with their component suppliers – have been “raising the bar” for lubricant performance through development of increasingly severe lubricant’s performance requirements along with more comprehensive field demonstration requirements to validate lubricant performance.
Second, wind farm operators are placing more emphasis on in-service oil monitoring to determine when oil has reached the end of its useful life, enabling them to maximise oil drain intervals and reduce downtime.
Offshore wind turbines
It is said that performance expectations for lubricants used in offshore wind turbines are higher due to demand for extended life.
Harrington says oil life is critical for both on shore and offshore installations.
“A balanced wind turbine gear oil must deliver excellent performance along several dimensions. Reducing wear in gears and bearings, both low and high speed bearings, is the primary role of wind turbine gear oil. In addition, the oil should have high viscosity index and good oxidative stability to maintain protection and deliver long oil life even when the gearbox operates at elevated temperature,” explained Harrington.
The viscosity of the oil at low temperature can impact the start up sequence of the turbine and oil with better low temperature performance may allow a more rapid cold start-up while reducing the risk of oil starvation at low temperatures.
The oil must be able to separate from both air and water and protect gearbox components from rust and corrosion, pointed out Harrington. A higher level of protection against rust in the presence of salt water is needed offshore.
“Wind turbine manufacturers and their gear and bearing suppliers have developed lubricant specifications based on existing industry tests for scuffing, micropitting, bearing wear, and so on. These requirements challenge lubricant researchers to develop lubricants with excellent, balanced performance. After a new wind turbine gear oil has shown excellent performance in a wide range of industry standard tests, its performance must be demonstrated under real-world conditions, in field trials,” said Harrington.
Replacing lubricant
State of the art condition monitoring and routine oil analysis are used by the wind farm operators to predict when a lubricant will need to be replaced.
This has two benefits, said Harrington.
First it allows oil changes to be planned rather than conducted on an unplanned, reactive basis. Second it allows these activities to be scheduled in a way that will minimise the impact of turbine downtime on power generation (that is by doing this work during low wind periods). In addition, state of the art condition monitoring can provide an early warning of increasing wear rates through measurements of ferrous particles in the oil or changes in the vibration signature of the gearbox.
“Unlike industrial gearboxes, an experienced mechanic doesn’t walk by the gearbox on a regular basis to look at the oil in the sightglass or check the vibrations from the gearbox – either quantitatively or qualitatively,” said Harrington.
Regarding the use of the correct lubricant, Harrington recommends that wind farm operators need to follow good lubricant storage and handling practices to reduce the probability of using the wrong lubricant.
Synthetic lubricants offer performance advantages versus their mineral oil counterparts, shared Harrington.
These performance advantages include: better film thickness at elevated temperatures and improved oil flow at low temperatures, superior oxidative stability, reduced traction, and others. The advantages have the potential to impact wind farm O&M costs by extending gearbox life, reducing costs and downtime for oil changes, and improving energy efficiency. Also, extended oil drain offers safety and environmental benefits through fewer trips up-tower and reduced waste oil generation.