Optimising annual energy production with apt handling of yaw misalignment
Wind energy companies are getting better at understanding what induces yaw misalignment and the related impacts on lost energy and lost revenues.
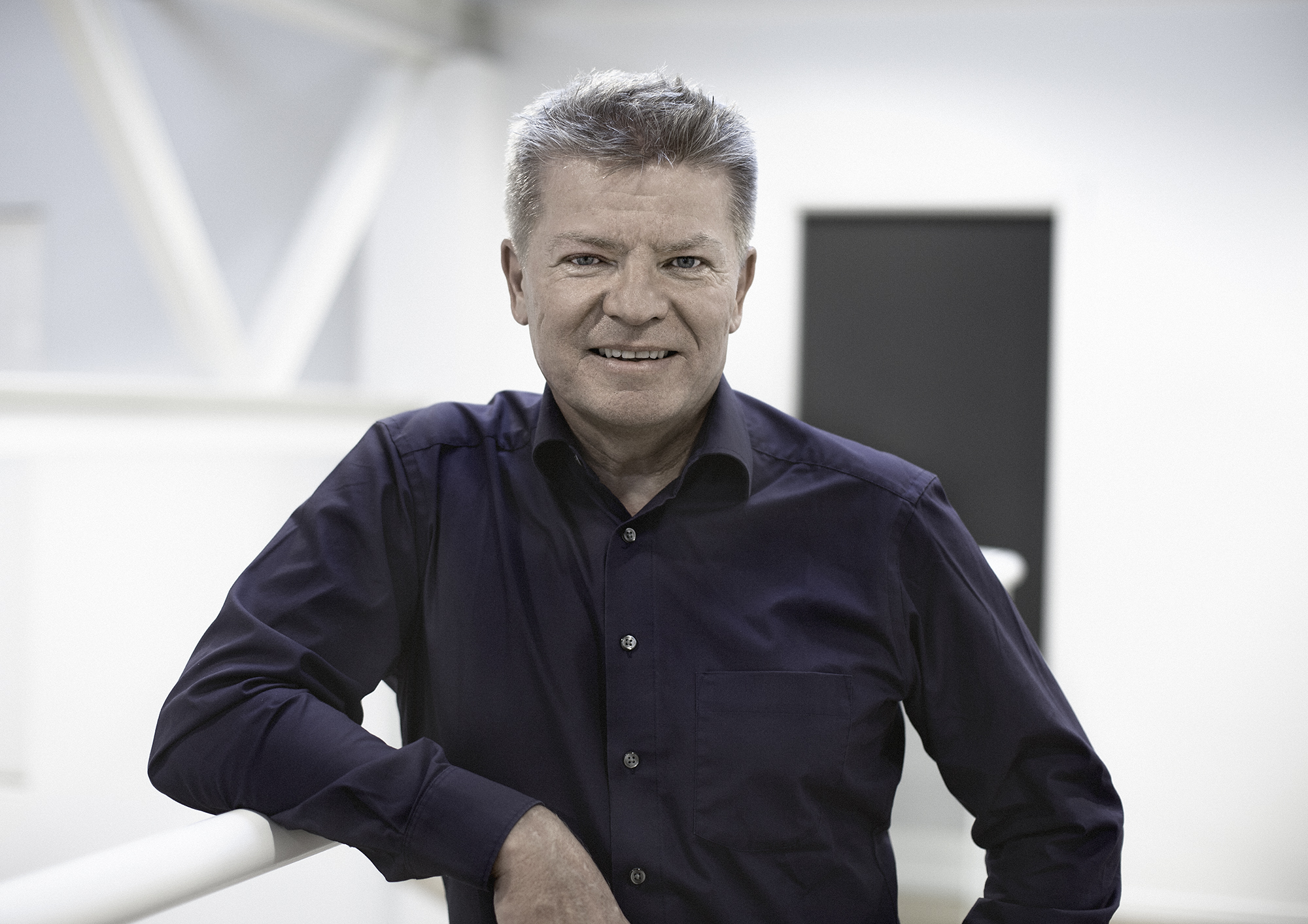
The wind industry as a whole is starting to comprehend the magnitude of the problem related to yaw misalignment. Prior to the emergence of the current crop of measurement tools, it was difficult to detect the problem with solid conviction as to its exact characteristics on any given wind turbine.
Specialists point out that yaw errors do not only induce a significant amount of energy loss, they are also causing a lot of additional stress loads on the critical components of the turbines causing premature wear and tear and accelerating the maintenance cycle. Premature wear and tear and shorter maintenance cycles cause a significant amount of revenue loss for the owner/ operator due to downtime of the turbine in addition to the actual cost of the components and maintenance.
Owner/operators, as Evan Osler, Sr. Technical Account Manager - Remote Sensing, Renewable NRG Systems explains, should recognise that they may be leaving substantial revenue on the table as well as causing unnecessary fatigue loading on their turbine components due to a problem which is now detectable and correctable, and also that it may not be possible to accurately diagnose turbine underperformance let alone yaw misalignment just through turbine SCADA intercomparisons or physical checks of turbine control vane alignment. Turbine control anemometers meanwhile are only as accurate as the specific transfer function that has been established to compare them to the freestream wind.
Inaccuracy vs. uncertainty
Dr. Samuel Davoust, Head of Product and Technologies, Avent Lidar Technology says that it would be a stretch to say that turbine wind sensor equipment is not capable of providing wind turbine owners with wind direction data. It is important to understand that wind turbine sensors are validated equipment which have, as any instrument, an inherent uncertainty.
“This uncertainty shouldn’t be mistaken for inaccuracy,” he says. He adds that they have some limitations as they are placed directly on the nacelle. Due to this position, the wind sensors are affected by complex aerodynamic effects such as the rotor blocking effect and blade passage. Usually, the sensors are initially calibrated to account for these effects and to deliver the correct wind data to the turbine. For example, the free wind. As for any instrument, calibration functions should be regularly checked to avoid any drift over time.
However, Søren Mouritsen, CEO, ROMO Wind says, “...no turbine equipment on the face of the earth can provide yaw misalignment data. They can only provide wind directions – which is what is being used to control the yaw – but their readings are inaccurate due to rotor turbulence. There is no way you can make a transfer function correcting for turbulence. The yaw misalignment constitutes the deviation from the correct turbine position”.
What causes yaw misalignments?
Mouritsen explains that more than half of all turbines have average or static yaw misalignments. He explains that there are several explanations for this. First, it is very easy for service technicians and turbine installation staff to accidentally induce a yaw misalignment when exchanging or installing the wind direction sensor. A wind vane only has to be misplaced by very few millimetres in order to induce a major yaw misalignments, e.g. a 5-6 millimetre turn of some wind vanes induces a 15 degree yaw misalignment causing 5-6% annual energy loss. Since the turbine owner has no way of monitoring the yaw misalignment problem which occurred, one never discovers or understands the resulting and very significant revenue losses and at the same time significantly increased loads on the turbine.
Secondly, the terrain and other wind turbines in the turbine environment can also induce yaw errors. The turbine manufacturer of course did its best to find the right wind sensor offset when developing a new turbine model, but it had no way of adjusting to the actual sites, where the turbines were subsequently installed.
Finally, there can be a mixture of causes. For example, any change in the nacelle air flow and measuring conditions for the turbine sensor, can immediately induce yaw misalignments.
Estimating Loss
The annual energy production loss due to yaw misalignments increases with Cos2 – and not least important – so does the wind turbine loads. So larger yaw misalignments can be devastating to the wind turbine project economy, says Mouritsen.
The entity has to date completed analysis of 67 randomly selected, onshore wind turbines with its iSpin technology – new and old – and almost all located in flat, non-complex terrain. According to Mouritsen, six out of 10 of the turbines had more than 4 degrees average yaw misalignments, and for this reason alone the owner can expect 2% more annual energy production from a wind farm. The statistics don’t show any tendency towards newer turbines having less frequent yaw misalignments than old turbine types.
In addition, it also been observed that all wind turbines had what the team calls dynamic yaw misalignments. For example, all turbines showed a variation of the yaw misalignment around the mean value of +/- 15-25 degrees (even if the static yaw misalignment was zero degrees).
“This is quite surprising because most turbine manufacturers claim their turbines only to have a +/- 5 degree dynamic yaw misalignment. This may also be true in a nice wind tunnel prototype experiment, but it is apparently very different in the field. Again, this is because technology for yaw misalignment detection is still not used as a routine in the industry,” says Mouritsen. He believes that dynamic yaw misalignments can be significantly improved, and with further revenues and load reduction to be gained as well.
However, at the same time, a section of the industry also points out that this is subject of to a debate in the industry and experts question the amount of additional benefits gained with dynamic yaw once the static yaw is corrected. There is a consensus on the fact that improved free wind measurements allow load reduction by optimised pitch and yaw actions.
Functioning
Technology has been developed measure free wind, such as The Wind Iris from Avent, a turbine-mounted Lidar that directly measures the undisturbed free wind – from 40m to 400m - outside of the rotor blocking effect and provides data such as wind speed, direction, and turbulence intensity. The instrument is versatile since it used not only for yaw misalignment detection, but also for other analysis: such as power curve measurements, nacelle anemometer calibration and turbulence and wake analysis. The offering has been designed to measure with an equivalent accuracy as the IEC61400-12-1 power performance measurement standard.
Davoust says a major progress in this arena has been the release of the first independent power curve measurement procedure for nacelle-mounted LIDARs, following a three-year project (with a consortium featuring DTU Wind Energy, Dong Energy, Siemens Wind Power and Avent Lidar Technology, funded by the Danish Energy Technology Development and Demonstration Program (EUDP)).
The Wind Iris is already in operation on a number of projects for power curve measurements, including Dong Energy’s 367 MW Walney offshore wind farm, located in the Irish sea.
“Offshore and in complex terrain, the main benefit of turbine-mounted Lidar is that it removes the need for a met-mast, which can be a very expensive equipment in this these environments. They allow for accurate and affordable measurements, resulting in reduced cost of energy and increased competitiveness,” says Davoust.
He adds that turbulence intensity and more specifically wake analysis is also a key topic for the offshore wind industry, as the wind farms are bigger than onshore. One of the leading programmes in this area is the industry funded programme run by the UK Carbon Trust’s Offshore Wind Accelerator aiming to reduce the cost of offshore wind energy by 10%. Its wake research section uses four Wind Iris nacelle-mounted Lidar and two ground-based scanning Lidar.
Of course, yaw misalignment correction is also an area of interest. This concerns more for the onshore industry for now as the offshore industry is focused on other topics such as logistics, installation and wind farm layout. It is important to note that this problem is not only linked to yaw measurement errors and operators have to analyse many parameters to optimise their assets.
This, according to a specialist, is illustrated in the research area where campaigns often include yaw misalignment as part of a wider research topic. For example, the LAWINE - Lidar Applications for Wind Farm Efficiency - project is focused on power performance validations with Lidar, yaw misalignment, blocking effect and vertical wind shear (includes ECN research center, turbine manufacturer XEMC Darwind and Avent Lidar Technology).
Lastly, it should also be noted that wind turbine manufacturers are aiming at ever-optimising their products and sensing technology is part of their effort. They have established industrial development programmes to improve this on next-generation wind turbines, and Lidar technology is part of this effort, he says.
Being proactive
Alex Woodward, Head of Marketing, ZephIR Lidar highlights that currently turbine control is still largely reactive. This refers to the fact that the yaw and pitch control adjustments will be made after the wind hits the turbine, for example, the stress loads measured on the blades or traditional wind sensors (combined with historic data and information gathered from nearby metmasts). He says Lidar measurements provide data regarding the wind before it hits the turbine and this way one can protect turbines from potentially harmful events.
This shift to proactively control has already occurred in the aerospace industry and has led to major improvements in that industry.