Does your O&M supply contract really meet your long-term requirements?
Frequently, an O&M contract is judged by its bottom line costs, however this is not the only factor that a contract should be gauged against. We look at the different strategies and approaches so that you can assess which is the best fit for your...
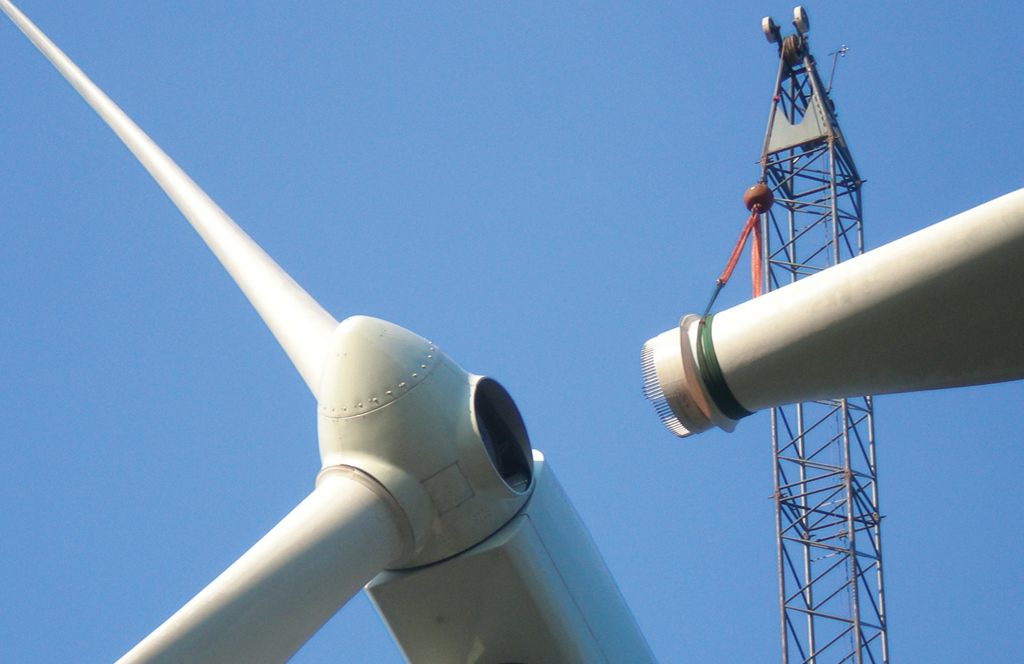
By Ritesh Gupta
Owners and operators of wind farms have a due diligence requirement to perform a detailed gap analysis to ensure the scope of operation and maintenance supply contracts will meet the requirements of their long term O&M programmes and will ensure safe long term operating availability of the turbines.
There are many factors that should be considered when deciding which solution is best for the owner and operator in terms of their long term O&M. These include the risk willing to be assumed by owners and operators; OEM performance during warranty period; Available funding within the project; Level of desire by the owners and operators to learn and understand operation and maintenance functions; and Initial turbine supply agreement deliverables.
Lifecycle-driven strategy
To ensure that an O&M contract meets the scope of supply, there must be clearly understood agreement by all parties. This is why a gap analysis should be performed to ensure the scope of supply meets the project requirements.
Alex Potier, director of sales, Broadwind Services, says owners need to ensure that operations and maintenance activities are conducted in accordance with the procedures and timeframes defined by the turbine OEM. He adds that this information is typically provided in the Operations and Maintenance manual and helps ensure that the equipment is cared for within the original design specifications.
“Owners should also develop a lifecycle-driven strategy around turbine platforms and specific components, gathering empirical performance data throughout the project lifecycle. By comparing this information across fleet-wide data, owners can also better anticipate more at-risk components, failure rates, and mean time between failures, and this can allow owners to better negotiate key contractual terms around specific issues,” says Potier.
In addition, interests should be aligned between both parties as much as possible, and operators should be incentivised to minimise turbine downtime and maximise equipment performance.
Service agreement
Dan Shreve, Partner at MAKE Consulting, indicates that the scope of the inspection should reflect the scope of the service agreement.
“Conducting an expensive vibration and borescope inspection makes little sense if the turbine OEM is providing a bare bones, two-year, scheduled maintenance only contract. In that situation, the asset owner may be better off investing in a long term CMS solution,” he says.
“Conversely, with a long term, full service agreement in place the asset owner has recourse to the turbine OEM for major repairs and should perform a full drivetrain inspection. I wonder if many turbine OEMs have thought about the impact of EOW (end of warranty) inspections at year 10 or year 15.”
End of Warranty Inspections also must be handled diligently. Bill Jacks, director of operations and maintenance, director of quality, Gemini Energy Services, says a thorough and comprehensive EOW inspection should include a full turbine walkdown and visual component inspection, an infrared thermography inspection, vibration monitoring, and gearbox oil analysis.
“Infrared thermography is the use of an infrared imaging and measurement camera to see and measure thermal energy emitted from an object in the turbine. Vibration monitoring is carried out by installing sensors on the gearbox, generator, and main bearing with the goal of detecting potential failures on bearings and teeth while the turbine is in operation. An EOW oil analysis will check the chemical and physical make-up of oil taken from the turbine hydraulic system and gearbox allowing the owner to potentially catch a premature failure of the component,” explains Jacks.
Owners, based on the information are therefore encouraged to go for a complete EOW inspection to protect their investment and prolong the longevity of the turbines and their systems.
Choosing the best fit (before the negotiations)
Jacks points out that more times than not a contract is judged by its bottom line costs, however this is not the only thing a contract should be gauged against. An owner should not always run with the cheapest bidder, but with the company or ISP that has the best fit for their project.
He recommends that before getting too deep in negotiations with the OEM or an ISP, the owner should evaluate their post warranty goals as they may have changed as the project matured. Do those goals and objectives line up with the potential companies being considered? This will be the single most important step in moving forward, says Jacks.
“OEM’s are chosen by owners sometimes because it feels like a safe decision. Who better to operate the turbine than the company that built it? ISPs are sometimes chosen because of how many other contracts or MW they have under their belt. They have a ton of other turbines so they must know what they are doing, right?
“Finding that “fit” for your project’s goals and company are a much smarter choice in the long term. Make sure and look past the major points of an O&M contract such as availability and price to really dig into the small details. Those will be the life blood of your contract for the period signed,” he explains.
Post-warranty costs
As for coming to grips with post warranty costs prior to post warranty operation, one of the main things an owner has to come to terms with is: O&M costs rise as turbines age. Jacks elaborates on this further and says more than likely an owner’s wind farm has been in operation five years or more before the warranty expires, however most modern day turbines have a 20-year lifespan or longer.
He says that is a large chunk of time to operate in the post-warranty period and as time goes on, the yearly costs will escalate including the frequency of unscheduled corrective maintenance, component failure and replacement, and wear and tear. One way that owners can help offset those costs, is with a competent post warranty ISP; they will have the knowledge and experience to forecast and plan for such events by properly maintaining and operating your project into this new phase of its life cycle.