Solar tower ISCC: Stacking up the benefits
In the first of a two-part series, Juergen H. Peterseim explains how integrated solar combined cycle using solar tower technology can make CSP commercially viable.
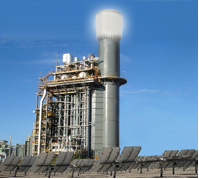
By Juergen H. Peterseim in Sydney
Concentrated solar power (CSP) has made large progressive technology leaps in the past decade. However, its levelised cost of electricity (LCOE) continues to price it out of the market. According to the International Energy Agency's Technology Roadmap 2010, costs are expected to be around AU$200/MWh (US$208/MWh) in 2015.
This contrasts starkly with the cost of alternatives such as wind and biomass. According to a recent report by the Australian Academy of Technological Sciences and Engineering, by 2015 onshore wind will cost around AU$100/MWh (US$104/MWh) in 2015, and biomass, around AU$60/MWh (US$62/MWh). Cost reductions are therefore essential if CSP is to be implemented with fewer - or without - government subsidies.
Hybridising CSP with other fuel sources is an attractive option for implementing low-cost CSP capacity. Several coal and gas-fired plants hybridised with CSP are already operational and the world’s first CSP-biomass plant is currently under construction near Barcelona, Spain.
Hybridisation delivers multiple major benefits. Depending on location and size, ISCC plants can reduce LCOE immediately by up to 30% through the joint use of equipment, such as steam turbine and condenser. Bolting new technologies onto traditional technologies flattens an otherwise steep learning curve for technology providers, operators and financiers, which in turn enables quicker plant implementation.
Other advantages include a relatively high capacity factor without capital intensive storage; meanwhile, an ISCC plant's lower DNI requirements (≥1,700kWh/m2/year), enables CSP plants to be installed closer to load centres. The host plant can compensate DNI variations easily, while small CSP projects for industrial power and heat supply become viable through lower investment requirements and financing risk.
The conversion of open cycle gas turbine (OCGT) and combined cycle gas turbine (CCGT) to ISCC plants would reduce investment requirements significantly. This is because major equipment items, such as gas turbine and plant control system, are already on site.
Sub-optimal deployment
Currently, a number of ISCC plants are operational in the US, Egypt and Morocco. Further plants are either being investigated or are already under construction in Iran, Morocco, and India.
The largest ISCC unit in operation is the 75MWe Martin Next Generation plant in Florida, USA. All of the existing hybrid plants use the mature parabolic trough technology with thermal oil, providing saturated or slightly superheated steam to the heat recovery steam generator (HRSG), where further superheating to steam turbine requirements takes place using the hot gas turbine exhaust.
This concept is well proven in several plants but requires both steam generators to operate simultaneously, limiting the solar contribution to typically less than 15%. The likely reason for choosing the parabolic trough technology with thermal oil was financial risk mitigation. However, the technology selection comes at the expense of steam temperature limitations of less than 390°C. This limitation is caused by rapid thermal oil degradation ≥400°C.
Developers should instead be looking to solar tower technology. With more solar tower plants commencing operation and construction around the world, such as Gemasolar in Spain and Ivanpah in the US, the technology is increasingly viewed as mature and bankable.
Significantly higher steam parameters (≥540°C & ≥ 140bar), compared to parabolic troughs allow simple and highly efficient integration into the high pressure, high temperature CCGT steam cycle. Both steam generators are able to operate independently as the CSP and HRSG system provide identical steam parameters to the joint turbine.
In addition to sharing the steam turbine and condenser, solar tower ISCC plants enjoy the benefit of sharing building infrastructure. The main stack for example can be modified to support the solar receiver. Stack heights over 100m are common and provide a good cost-saving opportunity, as the tower in a stand-alone plant requires approximately 5% of the total investment.
To ensure efficient steam turbine operation with the CSP plant offline, the solar tower capacity should match the HRSG steam capacity. With this combination, the steam turbine would always operate in the efficient 50-100% load range.
Sizing up storage
Adding thermal storage has the potential to increase the solar contribution. However, its commercial viability depends strongly on the value of energy dispatchability. Historically, electricity demand is higher during the daytime and that is when the solar plant can provide the additional capacity needed.
At the 200MWe scale, CCGT plants realise overall efficiencies of 55% resulting in a very efficient use of natural gas compared to back-up boilers in traditional CSP plants. Larger units could realise up to 60% conversion efficiency. Typically, ISCC plants operate in high ambient temperature environments, which reduce the gas turbine (GT) efficiency. To keep the GT efficiency high, low-temperature CSP heat could be used to chill its inlet air.
The capacity of the CSP plant is mainly driven by the part-load efficiency of the steam turbine. A 100MWe steam turbine remains efficient down to 50% part-load. With the HRSG providing sufficient steam to generate 50MWe base-load, the steam turbine would be operating at a good efficiency during the night with power peaking at 100 MW at daytime through additional CSP steam.
Using thermal storage would allow a larger solar contribution, when night-time energy could be drawn from the storage tanks. However, the economic viability of thermal storage strongly depends on the value of energy dispatchability.
To optimise the heliostat field size and avoid optical losses due to mirror wobble, the heliostats are arranged in a 320° circle around the plant, with the main stack in the centre (Figure 2). A 360° heliostat field is not possible due to the arrangement of other plant components, such as HRSG and condenser.
The main stack in this scenario would need to be approximately 30m higher than required for a stand-alone CCGT plant to ideally locate the solar receiver. Steam turbine, cooling towers, buildings etc are arranged adjacent to the main stack / solar tower. The ISCC plant could be either air or water cooled with air-cooling being the more likely option considering water scarcity in remote sites.
The carbon dioxide intensity of the proposed ISCC plant is 365kg/MWh which is 60% lower than the 2005-07 Australian generation portfolio average. Using 15 hours of full load thermal storage has the potential to further reduce the carbon intensity to 308kg/MWh. Depending on the remoteness of the site and infrastructure availability the levelised cost of electricity for such an ISCC plant can vary from AU$140-180/MWh (US$145-187/MWh).
ISCC plant siting in Australia
ISCC plants are a promising transition technology for Australia with abundant natural gas reserves and excellent solar conditions.
Typically, a direct normal irradiance (DNI) of ≥2,000kWh/m2/year is required for stand-alone CSP plants but due to ISCC cost reduction benefits, such as joint use of equipment, regions with a DNI of ≥1,700kWh/m2/year and natural gas resources can be considered.
In Australia several locations in Queensland, New South Wales, Western Australia, and South Australia fulfil these criteria. Most of these sites are remote or off-grid with significantly higher electricity prices than the national average, which is one of the lowest of all OECD countries. In addition natural gas prices are expected to increase significantly over the next years due to large LNG export facilities coming online. This will favour the use of CSP systems as fuel saver systems.
ISCC plants are ideal for sites with a high DNI, natural gas abundance and a requirement for low cost reliable power all year round. The hybridisation of CSP technologies can reduce capital expenditure significantly, allow the construction of reliable low carbon intensity power plants today without significant or indeed any government subsidies.
Enabling more private investment will allow CSP technology suppliers to ramp up manufacturing capabilities and reduce cost through learning experiences. Operators and financiers currently inexperienced with CSP installations could familiarise themselves with the different technologies available and build up expertise.
Remote sites suffering from high electricity prices stand to benefit from ISCC plants particularly when open cycle gas turbine / engine plants are the current source of power generation. Reducing the carbon intensity of power generation by a potential 60%, compared to the 2005-07 Australian generation portfolio average, is significant and would help Australia, and other countries, to meet emission reduction targets at low cost while continuously growing a CSP industry.
The second part of this series will present a 200MWe solar tower ISCC example and the ideal locations for ISCC plants in Australia.
To respond to this article, please write to the Editor:
Rikki Stancich: rstancich@csptoday.com
Image credit: Institute for Sustainable Futures, University of Technology Sydney