The solar field: Key to driving down CSP tower costs
A look at the global project pipeline indicates that towers are destined to play an increasingly dominant role in the CSP landscape.
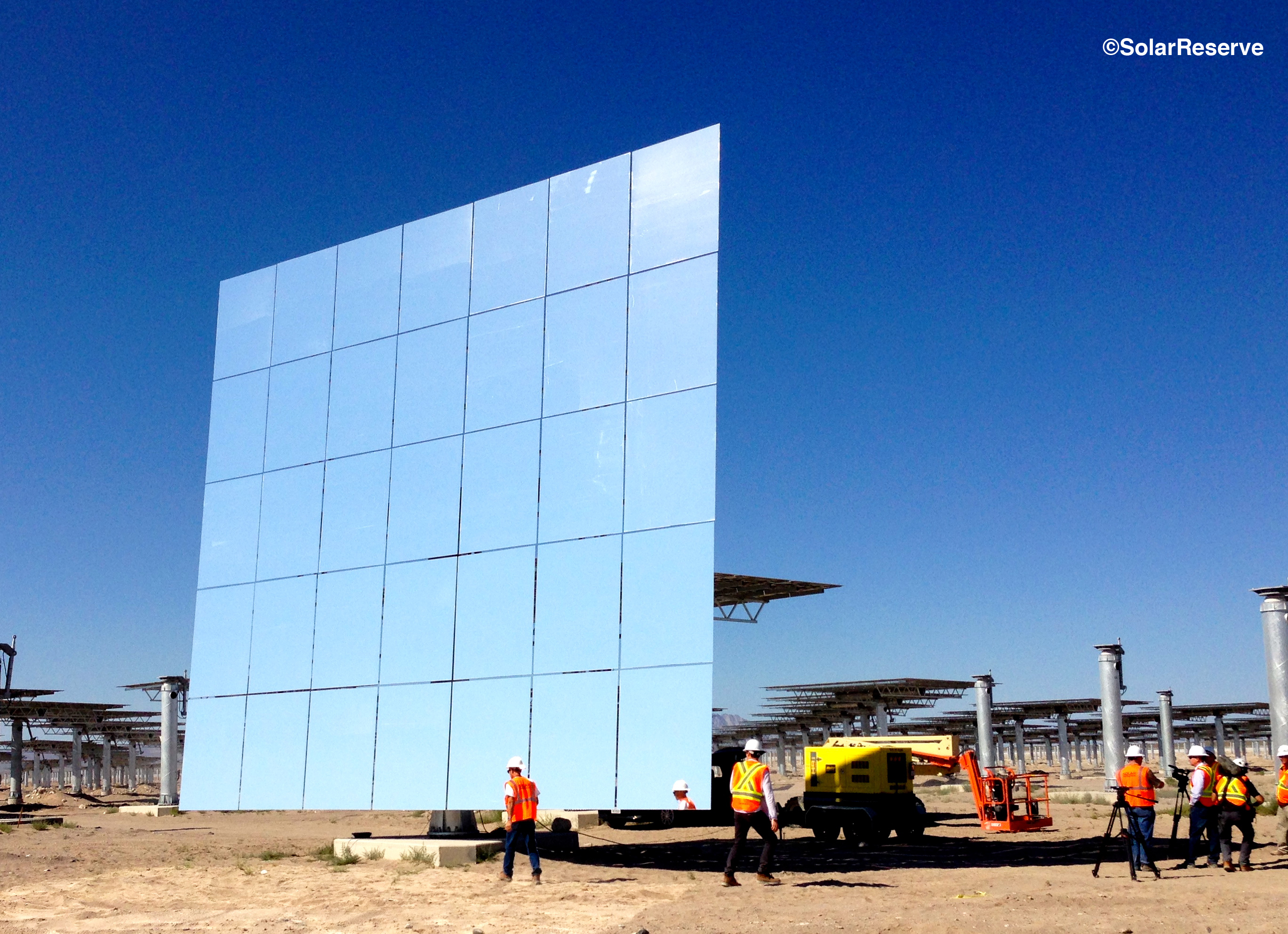
According to data available on the CSP Today Global Tracker 2014, towers account for 31 % of the global MW capacity under construction and for a staggering 42 % of the global MW capacity under development.
By Ángela Castillo.
Among the most compelling reasons for its adoption are higher operating temperatures in comparison to parabolic troughs. However, some industry experts indicate that towers have yet to experience the cost reductions needed to make it attractive to deploy at a larger scale.
In order to unveil the most important developments in CSP tower cost reduction and optimization strategies, CSP Today spoke to tower developers and technology and component suppliers. Unsurprisingly, the solar field –including the heliostats, drives, foundations, pedestals and support structures – ranked first in the list of areas most likely to experience the highest cost reductions.
However, sources such as SolarReserve, ACS Cobra, schlaich bergermann und partner and Flabeg FE GmbH have predicted different cost reduction percentages in the CAPEX of tower plants over the next years. They are dependent upon the adoption of wireless heliostats, the reduction of the assembly and erection costs, and improved heliostat performance, among other factors.
Wireless heliostat = significant cost reductions?
Kevin Smith, CEO at SolarReserve, a solar tower developer and technology provider, firmly believes that the heliostat field will be subject to important cost cuts as a result of improved design and development advances.
“The heliostat field can account for 40 to 50 % of the project CAPEX, and we expect to see a cost reduction of around 40 % in our next project. The key factors for this to happen are overall improvements and efficiencies in the design of the structures, control systems, and the mirror facets,” Smith says.
In a project such as Crescent Dunes, with a CAPEX of USD 983 million (a 110 MW molten salt tower in Nevada, U.S.), the cost of the heliostat field would amount to in between USD 393 and 491 million. “The Crescent Dunes’ heliostat is a fully wired one. So every single heliostat in the field of over 10,000 heliostats has control wires that run underground, which is similar to installing a distribution system for a small town of 10,000 people, where each house has a wire that runs to it,” Smith explains.
Indeed, the company is working with the Sandia National Laboratories to test improved designs in individual heliostats scattered throughout the field. Smith believes that the heliostat field of the next generation is going to be “wirelessly controlled and potentially self-powered with distributed PV”, which would save costs related to the control wiring.
Could this be implemented in the near future? Smith believes so: “We are actually getting pricing quotes for our next heliostat field that shows that kind of cost reduction.”
Nevertheless, not at all experts consulted are equally enthusiastic. Gerhard Weinrebe, associate at schlaich bergermann und partner, a Germany-based consultancy firm and technology provider, believes that, indeed, the way forward is a wireless heliostat but doubts the potential it has to produce significant cost reductions.
“There are already smaller wireless units in operation in Germany and South Africa and I think that it will be available in the next CSP tower plant but it will only lead to a single digit cost reduction percentage,” he notes.
On the other hand, Alberto R. Rocha, Manager of Strategy and Business Development at ACS Cobra, offers a significant overall cost reduction figure: “Considering the solar field represents up to 45 % of the CAPEX of a tower plant, I believe cost reductions are likely to be at least 30 % within the next five years.”
The solar field at the Crescent Dunes site. Picture courtesy of SolarReserve.
Mirror costs
Paul Nava, General Manager of Engineering & Technology at Flabeg FE GmbH, a manufacturer of high-tech glass and mirrors, refers to a presentation delivered at the CSP Today Sevilla 2014 conference.
“The cost of the mirrors in a heliostat design makes up between 8 to 9 % of the total heliostat field cost. Considering the heliostat field represents around 45 % of a plant’s CAPEX, it would mean that a mirror cost reduction of about 10 % would lower the total CAPEX by 0,38 %”, Nava explains. Taking Crescent Dunes’ CAPEX as a reference, that would represent around USD 3,7 million.
Optimization and cost-reduction
Weinrebe highlights the importance of having a holistic approach that considers both the potential a component has for experiencing cost reductions and the resulting increase in overall efficiency.
“Although it may seem obvious, it does not make much sense to compare heliostats on a cost per square meter basis, because you have to take into account the heliostat optical quality and geometry. Therefore, when comparing two heliostat designs, you might have a slightly more expensive heliostat in terms of dollars per square meter, but one that is able to provide higher optical quality and tracking accuracy, and it may be the more cost effective one,” Weinrebe says.
Nonetheless, he does predict a reduction in the solar field CAPEX of around 11 % compared to the most cost-effective solution available today, which will depend on “higher optical efficiency, reduction of drive costs and a new structural system.” Expected reduction of LCOE will be higher due to improved heliostat field performance, meaning smaller receivers will be available. This in turn will reduce cost and thermal losses and, therefore, increase power generation.
“The heliostat field and receiver must not be considered and optimized individually, but as two closely interrelated system components,” Weinrebe explains. He also emphasises the importance of adopting a mass production system, similar to the one used in the automotive industry, to drive costs further down. “The next stage for cost reduction is working on the commoditization of the components,” he states.
The heat transfer fluid system and the power block
These are the areas where the experts believe less significant cost reductions will occur. “We are looking at advancements on materials that we can use as alternative heat transfer fluids, but we do not see that changing in the near future,” says Smith.
However, Rocha is of the opinion that this will only happen provided a disruptive material erupts. “In fact, there are many companies and research organisations already working on that and I would not be surprised to see it coming down within the next couple of years. However, bankability of such product would be an issue to consider,” he says.
With regards to the power block and the auxiliary systems, Smith believes they have been fully optimized over the years which would make further price cuts unlikely. “There might be some modest improvements in the steam turbines, but it would be a very small cost reduction,” Smith notes.
It seems that the solar field offers the best opportunities for overall cost reductions at CSP towers in the next years. However, it is important to consider efficiency and overall output of the plant to identify the components with the highest potential.