Skyfuel: Blazing trails with blue sky thinking
CSP Today speaks to Skyfuel’s CTO Randy Gee about the company's latest product upgrade and why
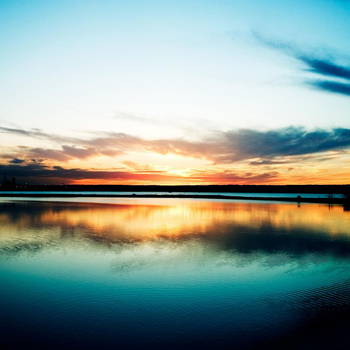
Related Articles
Interview by Rikki Stancich
The year 2011 will go down in Skyfuel’s annals as a memorable one. The company brokered supplier deals in several key emerging markets, it set the bar on product performance tests, and rounded off the year with a major product upgrade.
The company kicked off the year with a 12-month operations report from its installation at SEGs II. The results proved that the SkyTrough operates with a thermal efficiency of 0.737 at 350 °C, in keeping with forecasts established by the US National Renewable Energy Laboratory (NREL).
In March, the company secured two supplier deals, in China and India respectively.
The following month, NREL produced its accelerated weather test results for SkyFuel’s ReflecTech mirror film, confirming that the film maintains its high reflectance for 25 years’ equivalent ultraviolet exposure.
The ReflecTech film, which comprises multiple layers of polymer films topped with a layer of pure silver to achieve specular (mirror-like) reflectance, is designed to be manufactured at high volume, is unbreakable, lightweight, and costs up to 30% less than glass mirror reflectors. Such forward-thinking concepts are proving to be indispensable in the current, aggressive solar market.
In May the company signed a distribution deal in Italy, then two months later, walked away from CSP Today’s USA summit with the ‘Best Technology Supplier of the Year’ award tucked under its arm. In June, it inked a deal with Braxenergy to build CSP plants in Brazil.
Stamping out any question over its ability to compete with tried and trusted mirror technology, SkyFuel closed November with the launch of its abrasion-resistant ReflecTechPlus reflector film. The latest upgrade closes the last remaining gap between Reflectech and glass mirrors and firmly sets this cost-competitive, durable, easy-to-install product in a class of its own.
CSP Today speaks to SkyFuel’s CTO Randy Gee about the latest ReflecTech upgrade and about SkyFuel’s strategy to aggressively compete in new markets.
CSP Today: After subjection to an equivalent cumulative ultraviolet (UV) dose of more than 30 years of outdoor exposure, no degradation and no loss in reflectance were measured in samples of SkyFuel's latest abrasion-resistant ReflecTechPlus mirror film. How does this compare with glass mirror equivalents' performance?
Randy Gee: There is not enough data on the new glass mirrors to make a meaningful Service Lifetime comparison. Glass mirrors have changed in recent years – they used to be made with lead-backed glass, however this changed for environmental reasons.
So effectively, projects deployed in the 1980s and 1990s were based on a different set of glass mirror materials. More recent tests at NREL indicate that if you take away the lead backed coating, the glass mirror reflectance may decrease after a few years of outdoor service.
If glass mirror manufacturers have some further accelerated weathering test results, that would enable a better comparison.
CSP Today: Yet your own tests indicate that by applying an abrasive-resistant coating to the polymer mirror film, there is no loss in reflectance?
Randy Gee: We were worried at the outset that there would be a loss in reflectance with the addition of the abrasion-resistant coating, but it turns out there is none. The abrasion characteristic is a major plus – it’s a thin, transparent coating that is applied to the ReflecTech mirror film, which enables it to be cleaned using brushes without the risk of scratching or marring the film.
Brushing is a traditional an O&M practice for glass, but previously, was too abrasive for the ReflecTech mirror film. Until now, it hasn’t been a problem for our customers who instead use pressure washing. Rather, the decision to add the abrasive coating was a pre-emptive move to accommodate those accustomed to using brushes – for those more hesitant about changing their mirror-cleaning regime.
CSP Today: Which markets in particular was the ReflecTechPlus mirror film designed for? Was the anti-abrasion feature designed with, say, the sand storms of the Maghreb in mind?
Randy Gee: To be honest, we have never seen a polymer film - ours or others - scratched from a dust storm. This has always been a concern unsupported by real evidence.
However, our new abrasion-resistant coating should alleviate any concerns regarding the possibility. The real issue was abrasion caused by contact cleaning methods. So, in fact, ReflecTechPlus is designed for any market. Going forward, we will only use ReflectTechPlus on the SkyTrough.
CSP Today: 2011 has been a decisive year for SkyFuel. The SkyTrough has been proven at SEGS II, and there have been several major supplier agreements in India, Brazil, China and Italy. How does SkyFuel intend to service these markets: will you be shipping components; or manufacturing locally?
Randy Gee: If you design a reflector to be produced locally, it’s a different device that is especially easy to manufacture anywhere in the world with a minimum of shipped/imported components. We recognise that it is important for host countries to produce jobs via manufacturing content locally.
The things we would need to ship in would be rolls of ReflecTech mirror film, which in itself would be a fairly small volume; the drive/controls (which we call the ‘On-Sun unit’); and the receivers.
All the rest – the pylons, structures, space frames and torque plates, can be manufactured locally. The assembly and installation can involve local labour. The space frame can be extruded in the local country, whether it be Brazil, India or China.
CSP Today: What logistics challenges do these markets present when it comes to shipping and sourcing locally?
Randy Gee: The receivers are the only component that presents any sourcing challenge, given that these are only produced in a handful of places. ReflecTech mirror film presents an easy solution to reflectors, while the space frame can be produced locally.
The ReflecTech-based reflector really lends itself to high volume manufacturing – it entails a very simple manufacturing process that people understand well. You can effectively setup the reflector sheet processes anywhere – all you need is investment for an aluminum coil line, for coil unwinding and lamination. This presents a very modest up-front cost – in the thousands, as opposed to the millions.
We would set up in-country manufacturing of ReflecTech mirror panels for the SkyTrough, while we would have other components, such as the space frames, outsourced locally and delivered to the job site.
CSP Today: In terms of compliance, how challenging are the local content mandates in countries like India and Brazil for OEMs like Skyfuel?
Randy Gee: The localised nature of our product makes it easy for us to comply with the mandates. The mandates were also a strong driver behind our decision to have a largely out-sourced manufacturing model for the SkyTrough. It makes sense to boost the local economy. We find it easy to meet these mandates – it is a good fit with our outsourced manufacturing model.
CSP Today: What is next for the ReflecTech product?
Randy Gee: Going forward we will focus on increased specularity and adding an anti-soiling later to the abrasion-resistant layer. There have been a succession of improvements to the ReflecTech mirror film, and is only natural that we should continue to improve the product.
To respond to this article, please write to the Editor:
Rikki Stancich: rstancich@gmail.com