Heatcrete or Molten Salt?
This article is the first of The Expert Column Series, a space where two experts present their opinions on a topic proposed by CSP Today. This time, Juan Barragán (NEST AS) and Mark Schmitz (TSK Flagsol Engineering GmbH) discuss: Heatcrete or Molten Salt?
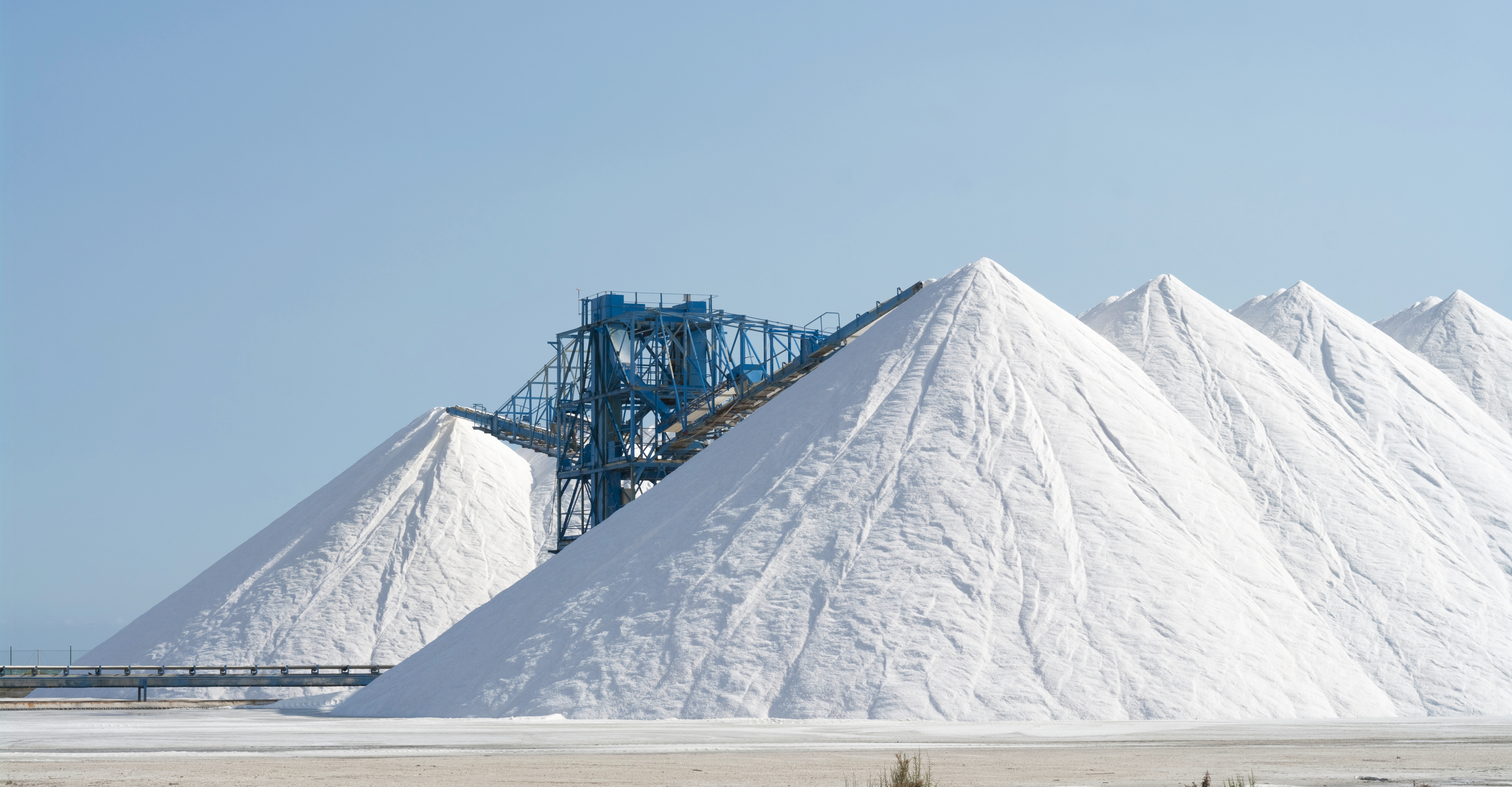
Heatcrete – Juan Barragán, NEST AS
Norwegian group NEST AS believe that their patented thermal energy storage (TES) technology, Heatcrete, is more competitive than other TES systems, including those based on molten salt. Here to explain why is Juan Barragán, Senior Engineer for Thermal Energy Systems at NEST, who holds a Master of Science in engineering with specialty in chemical industry process.
“At NEST AS, we have developed a new and cost-effective Thermal Energy Storage (TES) technology. This versatile solid-state TES system is applicable to Concentrated Solar Power (CSP) and other applications. Thermal energy is stored in a concrete-based storage medium developed in collaboration with Heidelberg Cement; Heatcrete. A storage system is made of a large number of individual elements that are connected together.
The HTF (same as used in the solar field) flows inside the Heatcrete elements, transferring the majority of the energy during the charge period or absorbing it during the discharge period. NEST’s technology enables a cost-effective, simple, fully modular and scalable system. Commercial size range may be from a few MWhth to several GWhth. Compared to molten salt systems, the NEST TES technology can be very cost effective for systems sizes in the MWhth scale.
The range of temperatures that could be stored within the solid-state storage ranges from subzero to higher than 600ºC. Such a wide temperature range is beneficial to facilities that use other types of HTF such as steam or new generation fluids. The wide range of permissible temperatures of the storage facilitates many different purposes, aside from prolonging the turbine generation, such us preheating the HTF, or power unit, in addition to ensure anti-freezing without any risk to the installation.
Cost efficient solution
The NEST storage system has less CAPEX than molten salt systems due to the simplicity and modularity of the design. Basically, the idea is to have the same unit repeated as many times as necessary to achieve the expected capacity. Avoiding external loops with pumps and different fluids it is possible to save a major part in the investment. Due to the solid-state storage medium, the amount of electrical tracing and heaters needed in NEST solution is also negligible compared to molten salt systems.
In terms of delivery and construction of a storage, NEST solution is also more competitive than other systems because a majority of the components for the storage can be locally sourced (mostly steel and concrete aggregates) in many regions around the world.
Furthermore, the NEST storage system has a lower OPEX because the main part of the parasitic loads come from the HTF pumps, and not the storage itself. The rest of the installation has very low electrical consumption. For this reason, the parasitic loads when the storage is in standby-mode is negligible. It is also worth pointing out that nearly all the components used are similar to what is typically used in solar plants; such as construction materials, instruments and valves. This alone dramatically reduces the spare parts inventory in a plant and the required training period for the O&M team.
Simple and robust design
The Heatcrete storage medium has been designed to be maintenance free. Standard concrete has proven to be a reliable material able to withstand millions of stress cycles during so-called proportional loading in the construction industry. In the case of a thermal storage, the Heatcrete will typically experience one cycle per day over the course of 30 years. This amounts to merely 10,000 thermal stress cycles over cycles over this period. This is considered low cycle fatigue so the expected life of the Heatcreate is much longer than the plant lifecycle. Welded steel pipes require also very low maintenance, so the main part of the maintenance should be focused in the interface between the storage and the rest of the solar facility. This is not the case for other TES alternatives.
The way to operate the system is very similar to the rest of the solar plant because all the elements managed during the operation are quite similar to the other components installed in the plant. Therefore, the same team with the same skills that operate the solar facility are able to also operate the storage system by simply varying the flow through the TES.
The design has a very flexible and robust performance, and as a consequence the shutdown periods expected for the NEST TES technology will be minimum, whereas long-term shutdowns could be expected working with molten salt systems due to the complexity of the fluid (salt plugs, corrosion, leakages, etc…)
Commissioning and first startup of the NEST installation is simpler than for molten salt systems. The initial heating is carried out by flowing the HTF through the storage previously conditioned with an external unit. This important phase, which is crucial for the performance of any storage, is easier to control than for the molten salt tanks with preheating and salt melting process.
Performance comparison
Analyzing the performance of the storage, NEST TES solution has very different performance in comparison to molten salt technology. The main difference is that the outlet temperature of the storage is going to decrease during the discharge and the inlet temperature is going to increase during the charge period, whereas for the molten salt systems both temperatures are constant.
This intrinsic performance gives the power output of the turbine a constant for molten salt and decreasing for NEST TES. In terms of gross production, the amount of electricity in a molten salt plant could be higher, but if we analyze the net value where parasitic loads consumed during production should be deducted it is possible to conclude that NEST TES has an improved performance. As a result of the sliding performance of the turbine working with NEST storage we realize that for certain period of time the performance of the turbine is also higher compared to a system using molten salt. This option can be utilized for projects where the PPA tariff is higher in the first hours of the discharge.
Making a decision about the best TES system is a complicated task, and it is necessary to analyze and evaluate several factors. For many of these, NEST storage is the most competitive alternative.”
Juan Barragán,
Senior Engineer for Thermal Energy Systems
NEST AS
Molten Salt – Mark Schmitz, TSK Flagsol Engineering
Mark Schmitz, Head of Technology and Innovation at TSK Flagsol Engineering GmbH, supports technology development for CSP plants at the German company, which has developed the conceptual design for the first commercial molten salt TES and now acts primarily as an EPC contractor. With experience in linear Fresnel collectors, parabolic trough plants, central receiver systems, and molten salt for storage and heat transfer, he explains why molten salt offers many benefits to the owner of a CSP plant.
“The central advantage of CSP over wind and PV is the dispatchability it owes to integrated thermal energy storage (TES) systems. The most mature and thus in power industry most wide spread TES technology system uses molten salts (MS). It was developed for Solar Two (1995), adapted for the use in line-focusing systems by a German consortium around Flagsol and first commercially used in Andasol 1 (2009). It is currently operating in more than a dozen commercial plants, including one tower system. The total storage capacity is sufficient to generate more than 5700 MWh of electricity each night.
Molten salt TES systems can be subdivided in direct and indirect systems. In direct systems the “cold” but still liquid salt is taken from one tank, acts as heat transfer fluid (HTF) by cooling the solar receiver and is stored in the hot tank, from where it is taken to generate steam on demand. In indirect systems a primary HTF (usually a sort of oil) is heated in the receiver and can parallelly heat a TES system or generate steam. In any case:”Panta rhei – everything flows” and heat transfer is achieved efficiently by convection. Heat conduction effects, that incur non-constant heat transfer, are negligible.
Nitrate salts, especially above 400°C require careful consideration of the material quality of containing vessels, pipes and pumps. This implies a strong economy-of-scale effect, i.e. the bigger the better, as the storage capacity, proportional to the tank volume, increases faster than the surface area. On the other hand hydrostatic pressure increases the tension in the tank walls with increasing height and diameter, resulting in optimal capacities of roughly 30,000 tons.
Obviously, this is no upper limit, as the Solana plant with six pairs of tanks shows. System sizes significantly smaller than the mentioned optimal size have increasingly higher specific costs. Another disadvantage is that such a system is not very flexible to change once it has been built, requiring thorough analysis of the present and future needs of dispatch.
TES systems based on molten salt offer a large number of benefits to the owner of a CSP plant:
- The specific storage cost is low. Nitrate salts are a bulk commodity and even an increased use by the CSP industry will not impact the giant amounts consumed by the fertilizer industry. The Andasol power plants, handicapped by porous supply chain and high engineering effort, could only be made economically viable through the implementation of a molten salt TES system.
- In storage systems based on molten salt the nominal discharge power and the nominal charge power are virtually independent of the storage capacity, depending only on the pumps that convey the hot salt or the cold salt, correspondingly, and the heat exchangers.
- Well-designed systems have a certain redundancy in some components so that even in case of the failure of a pump, the system can be operated with nominal performance. The level of reliability can be adjusted to the plant owners’ needs.
- As the masses of salt in both tanks are of relatively homogeneous temperature, the power for charging and discharging the TES system can be easily controlled by controlling the mass flow. The predominance of convective heat transfer results in the ability to operate the TES system from full to empty and vice versa at maximum power, whereas systems relying on conductive heat transfer, such as TES using solid or phase-change materials have a non-constant charge and discharge behavior. During discharge such systems either show a decrease in outlet temperature or only permit increasingly reduced mass-flows towards the end of the process.
- The systems are highly efficient. The HTF is only brought in contact with active heat exchanging surfaces – there is no flow through TES regions which are already (dis)charged. This keeps the pipe lengths short and the number of bends low. So we only see small pressure losses, and the electric consumption for charging and discharging is very low.
- Due to the round shape – molten salt TES tanks are cylindrical and have domed roofs - heat losses are low. The round-trip efficiency is 98% to 99%.
- Very small degradation in the capacity and in the heat transfer power is expected, none has been observed so far in the five years of operational experience.
- The large number of successfully operating systems allows easy access to financing.
In summary: Storage systems allow CSP plant operators to deliver electricity in a predictable manner and to optimally make use of variable feed-in-tariffs. Molten salt systems are proven technology and offer excellent bankability. As many studies and the CSP industry’s R&D activities indicate there is a strong trend to directly heat molten salt in receivers for all collector types – be it tower, Fresnel or trough – due to thermodynamic advantages the higher temperatures offer.”
Mark Schmitz,
Head of Technology and Innovation
TSK Flagsol Engineering GmbH