The design challenges of stop-start turbines for the CSP industry
One of the greatest challenges for CSP turbines is that, unlike turbines in the traditional thermal energy industry, they must be able to power up and down daily. What does this mean for the functioning and efficiency of a CSP plant? And what turbine-related technology advances can we expect to see?
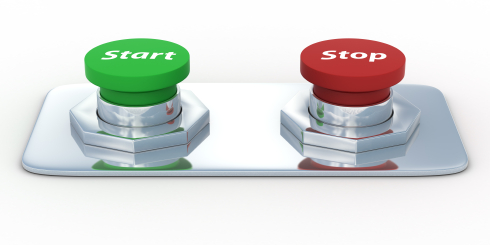
The oldest CSP turbines in operation, used to generate power in the longest-running CSP plant today - California’s SEGS plant built in the 1980s - are those supplied by Mitsubishi Heavy Industries (MHI).
“The daily start/stop of CSP steam turbines require design consideration of thermal stresses for the main components,” James Williams, MPSA Senior Vice President, North American Manufacturing and Repair Operations at Mitsubishi Power Systems Americas (MPSA) tells CSP Today.
“Turbines that support renewable applications, such as solar, operate under different loading conditions than turbines used for traditional power plants,” he points out.
“Turbines may cycle up-and-down daily at a solar generating facility, while turbines at a traditional coal or nuclear facility can operate continuously at full load for several months.”
To contend with this issue, MHI turbines at SEGS were designed to withstand more rigorous daily start/stop cycling. MHI uses an integrally shrouded blade design which has increased its resistance to stresses during starts and in operation.
Operations & maintenance lessons
Traditionally, turbines are designed to operate for five or six years continuously, when a service outage might take two or three weeks, and then to resume operation again for five or six years.
Once the steam is turned off, turbines start to cool down slowly, and after 48 to 68 hours, come to a low enough temperature that they can be stopped completely. So stopping takes a few days, although the restart can be done much faster, in several hours.
In 2011, California-based Field System Machining performed repairs in situ on SEGS, under Mitsubishi’s direction. “We performed a 100,000 hour major steam turbine inspection,” explains Williams.
“Mitsubishi disassembled the CSP turbine, removing the casing internals and rotor. Parts were inspected for steam erosion, impact damage, crack indications and general long-term serviceability. Repairs were made based on the inspection results.”
The five MHI turbines have now been in operation for over 25 years and are continuing to perform well. Siemens oldest CSP turbine, at Nevada Solar One in Boulder City, has been operating since 2007. These are the longest-running CSP plants, and their daily startups provide a challenge that traditional thermal energy plants don’t face.
The stop-start challenge
CSP Today asks Siemens’ industrial steam turbine department Director of Steam Turbine Development, Jari Nyqvist, why the nightly stops and starts cause problems.
“There’s two parts,” he explains, in an early morning call from Switzerland. “The first part is related to the fact that these stops make loading and de loading of components. It means from a mechanical integrity point of view - its cycling up and down - it means you are loading and de-loading components mechanically.”
“The major challenge is related to the big load pressure blades in the turbine, which are the most stressed part,” says Nyqvist. “They are in the exhaust, just before going in the condenser, the last stages in the turbine. That’s the part which is kind of limiting the steam flow capability.”
The second part comes from the fact that for part of the twenty four hours, you need to turn the turbines by turning gear for the rest of the night.
Nightly cool off
Although in CSP, the turbines are not generating at night, they are not turned completely off - to avoid real damage.
“The turbine is still turning slowly. Like one revolution per second or something like that,” Nyqvist explains. A small auxiliary hydraulic motor goes in and turns it slowly.
The revolutions have to be slow, to avoid overheating the bearing surfaces and also to avoid the shaft line becoming bent. If it stopped completely the shaft would bend.
What they would be concerned about seeing as a sign of stress would be things like wear in bearings’ surfaces, he says. “If the turbine is overstressed then a crack will occur somewhere. If you overload it from some respect, them it will crack and finally fail if the stress is continuing.”
A hotter future for CSP
“New technologies are allowing steam cycles to effectively operate with higher pressures and temperatures for improved turbine efficiency,” says Williams. Steam is at lower pressure in CSP compared to the 160 - 165 bars of pressure seen in combined cycle and 130-140 bars in traditional thermal plants.
The lower pressures and temperatures used in CSP untill now have tended to reduce the efficiency of CSP steam turbines. Therefore, finding ways to make it possible to raise the temperature and pressure are the future of turbine design, and the reason for the US DOE SunShot emphasis on these advances.
In tower applications, such as the BSE Ivanpah plant, which is due to power up this year with three turbines from Siemens, temperatures do come close to those of traditional thermal energy, which are between 540ºC and 565ºC.
“But now with tower technology and the molten salt, when it’s used as a fluid medium, it is coming slowly up to, I think, 540ºC,” Nyqvist estimates. “The Ivanpah plant is 540ºC."
“CSP is getting there. But trough, in particular, is limited to 400ºC due to the oil that they have in the oil system. The limitation is in the oil itself. For all the trough technology we have built, the maximum is 390ºC, I think,” he adds.
Back to the future
The higher operational temperatures and pressures is one of two big changes Williams sees coming. The other big change is energy storage.
“The two major developments in CSP steam turbines are steam conditions and energy storage,” says Williams. The addition of storage in the newer technologies means that turbines continue normal operation - generating electricity - for longer hours each day. This means there are fewer hours of being run in night mode.
In newer plants with storage - which is increasingly seen as an essential marketing advantage with utilities seeking more dispatchable renewables, in any case - CSP turbines will increasingly be operating under conditions more like turbines in traditional thermal industries.
The higher temperatures and pressures, along with the longer daily running hours from the inclusion of storage, mean that future CSP turbines will operate more like traditional turbines.
So, ironically, as a result of these developments, life will become easier for CSP turbines; not so much by solar-specific turbine design, as by other technological advances that recreate the environment of the much older traditional thermal energy industry: higher heat and pressure, and more continuous operation.