CSP cooling options: Workarounds for water scarcity
CSP Today speaks to Babul Patel, senior consultant at Nexant Inc., about the cost implication of plant cooling options and how to operate plants effectively under increasingly stringent water restrictions.
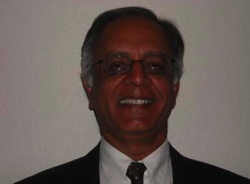
Interview by Rikki Stancich
CSP Today: For CSP developers, what is currently the best option for addressing the issue of water scarcity?
Babul Patel: When it comes to CSP planning, the biggest issue is the water resource, given that most CSP plants are located in arid areas. Permits and plans rely on access to and planned use of water. As such, availability of the water resource can be a limiting factor.
This has led people to look at alternatives for balance of plant and Rankine (steam) cycle cooling.
With dry cooling an air-cooling condenser eliminates 90% of the water requirement, given that the major usage is make-up water for the cooling tower water losses.
CSP Today: What impact does dry cooling have on the operational efficiency of tower and trough technology?
Babul Patel: The downside of air-cooled condensers is that on hot days, very poor performance of the air cooled condenser affects the turbine’s efficiency and output during a period when you would expect it to be operating at highest efficiency. In both tower and trough technology, the condensing temperature from the turbine exhaust is dependent on the ambient conditions. For wet cooling tower, it is the wet bulb temperature, whereas for the air cooled condenser it is the dry bulb temperature.
So on hot days, when market demand for energy is very high, the turbine is operating at reduced capacity and efficiency.
CSP Today: What are the cost-benefits of dry versus wet cooling?
Babul Patel: For dry cooling, the capital cost is higher than mechanical draft cooling towers but the operating cost is lower because you are not dealing with water - water treatment, and the discharge of waste water.
The operating cost is not that significant compared to the capital cost. In the past we costed out air-cooling at 2.5 times that of mechanical draft cooling towers.
CSP Today: Is there scope for those costs to come down?
Babul Patel: Not much. The majority of that cost is the total cost of material. A 100-200MW CSP plant cooling tower can occupy as much land as a football field. You need to provide such a large surface area that there is no way to cut down the material cost.
Some innovations are being made on structural improvment, using minimal support structure. As we learn more about the layout and structure there are some cost savings, but these are miniscule compared to materials costs that are dependent on commodity prices.
CSP Today: What other cooling options are considered viable?
Babul Patel: Engineers are looking at various options. One is hybrid-cooling using a 25% capacity wet cooling tower and 100% capacity dry cooling. In hybrid case part of the turbine steam exhaust is reverted to the wet cooling tower when ambient temperature rises.
This option improves efficiency compared to a 100% dry cooling tower, and with little loss of capacity. The wet cooling tower is only used on hot days, so you would use only 10% of the water that would normally be required by a wet cooling tower, given that you would only be using it a few hundred hours a year when the temperature is at a peak.
The dry-air cooled condensers see efficiency losses at around 90 degrees Fahrenheit / 32 degrees Celsius ambient temperature for about 40-60 days a year. This is the time you would take advantage of wet cooling.
CSP Today: But this doesn’t resolve the capital outlay cost issues.
Babul Patel: No. You still face the high capital cost outlay.
CSP Today: Given that water is such a constraining factor, is it likely that in future we will see more developers leaning toward Organic Rankine cycle (ORC) technologies?
Babul Patel: The Organic Rankine cycle is another low temperature operating system using an organic compound which uses steam turbine exhaust to vaporize organic fluid that is used in another turbine cycle. It operates at lower temperature, but reduces the cooling load of combined plant by as much as two-thirds of a conventional system.
It takes the steam exhaust from the Rankine cycle and uses that heat to operate an organic fluid. It’s a well-understood technology (it has been used in geo-thermal plants for years), so people are thinking “Why not apply it to CSP plants?”
Effectively you could piggyback the ORC on an existing system to increase the power generation of the plant and reduce the cooling requirement.
CSP Today: What impact would bolting-on a ORC have on overall project costs?
Babul Patel: In CSP plants, the capacity factor is low, at around 20-25% and the added capital investment for something that is used only a small amount of the time means that the return on investment is not attractive.
The solution would improve the overall CSP plant efficiency and would bring down the cooling load of the plant.
But nobody has actually done this yet, so it is not clear as what the extra cost would be.
CSP Today: How does wastewater use for cooling weigh-up and where would this option be viable?
Babul Patel: Waste water is a viable option that is being looked at for several developments in California and Arizona.
It is difficult to tap into, unless the plant is sited near a large community. In the Southwest US, the load centre and the CSP resource are in close proximity. In North Africa, on the other hand, most proposed sites are 50-100 miles from the coastal region, but most of the population is located near the coast. So these sites have no access to municipal water.
So it is an economical option, but you need to have a good source – to be located near a population center that generates a big enough volume of waste water.
CSP Today: What about the costs of developing the infrastructure required for treating and transporting the wastewater – how do these play into overall project costs?
Babul Patel: The costs are manageable. Here in the US, the municipality s responsible for treatment and disposal of wastewater – they have a cost item on their hands that they would be only pleased to find an end user for.
The treatment cost is not that significant, and if you can locate a CSP plant a few kilometers away, the piping costs would not be significant either.
A key issue with water use is its cost. In the southwest US people are waking up to the fact that water is a very valuable resource and that it is not convenient to see it evaporate in a cooling process. It is getting increasingly difficult to extract ground water for CSP.
CSP Today: What impact is the zero water discharge restriction having on costs and how can plant operators mitigate some of these costs?
Babul Patel: Most power plants are tending toward zero water discharge, where they have to treat and re-use water, which adds up to a significant capital and operating costs. So there is a need for minimizing water consumption.
We have started seeing a lot of new conventional (combined cycle and coal) plants permitted with zero liquid (water) discharge or ZLD, and who have seen an increase in their operating costs in order to achieve zero water discharge. Developers are forced to address this at the design-build phase.
Plants already permitted may have an easy time, but then again, they may not have the luxury of a 30-year plant life, as at any given time regulators could revoke the permit on the basis of new regulations.
Babul Patel will be presenting at the forthcoming CSP Yield Optimization Conference and Expo, to be held in October in Denver.
To respond to this article, please write to the editor:
Rikki Stancich: rstancich@csptoday.com