El proyecto HITECO presenta un innovador tubo receptor
Las plantas CSP de canal parabólico están limitadas en su rendimiento por la temperatura a la que se
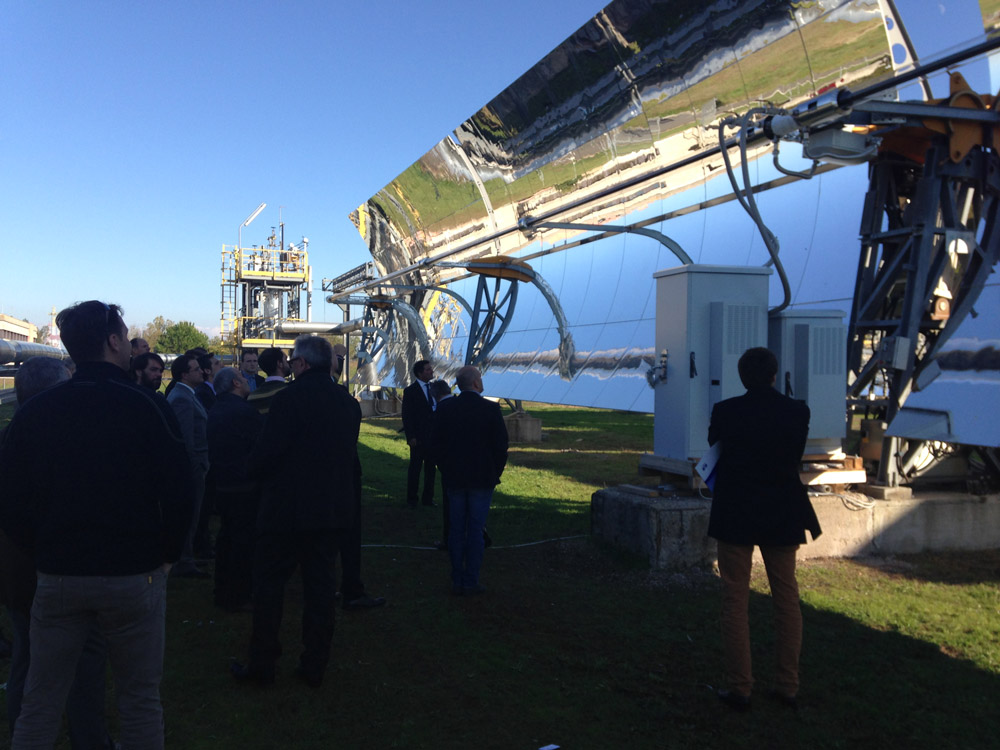
Para superar este límite, el proyecto europeo HITECO ha desarrollado un colector capaz de operar a temperaturas de hasta 600 ºC.
Por Jorge Alcauza
Formado por un consorcio de once entidades -cinco de ellas españolas- y liderado por Aries Ingeniería y Sistemas, el proyecto cuenta con financiación de la Unión Europea. El resultado de la investigación fue presentado en Roma el pasado 30 de octubre: se trata de un tubo receptor que puede suponer un avance significativo para la industria CSP.
HITECO ha trabajado tanto en el desarrollo del receptor como en su fabricación a escala comercial. Para conocer los detalles de la investigación, CSP Today conversó con Hugo Cachafeiro, director del proyecto y jefe de I+D del departamento de energía de Aries.
CSP Today: ¿Cuáles son los principales hallazgos de la investigación?
Hugo Cachafeiro: El nuevo receptor solar desarrollado por el proyecto HITECO cambia gran parte de los conceptos vigentes (…) Entre otras ventajas, el tubo ofrece un nuevo diseño que incrementa su fiabilidad y robustez. Esto impacta directamente en los costes de mantenimiento de las plantas.
Los hitos que han marcado la evolución del proyecto han sido básicamente dos: por un lado, la definición del concepto y diseño técnico, que resolvía las limitaciones que actualmente presentaba la tecnología. Y por el otro, la validación del diseño, tanto en laboratorio como en campo.
El tubo desarrollado se encuentra en fase de solicitud de patente en los EE.UU y la UE, mientras que en China ya le fue concedida. En definitiva, los avances están relacionados con la validación de los siguientes conceptos:
· Ha quedado confirmada la posibilidad de realizar alto vacío en una cámara colocada en el campo y mantenerla. Esto equivale a no tener que usar las típicas uniones GTMS (sellado vidrio a metal), sino las bridas metálicas y juntas de sellado poliméricas.
· El uso de gases aislantes permite trabajar a altas presiones y supone una reducción de la criticidad de las operaciones y un incremento de la robustez de la solución.
· Utilización de un vacío dinámico (en “batch” cada varios meses), que permite monitorizar el estado de las cámaras sin tener que usar ningún tipo de “getter”, con la reducción de costes asociada.
· El desarrollo de un nuevo selectivo solar, capaz de trabajar en diferentes condiciones e incluso con pequeños porcentajes de aire.
CSP: ¿Cómo han afrontado la unión vidrio-metal, un punto crítico de los tubos? ¿Se traduce esto en un incremento de producción y rendimiento?
HC: El rendimiento es mayor por dos motivos. Primero, la ganancia neta es mayor (mayor área afectiva) y en segundo lugar, la estabilidad y seguridad que ofrece a la producción, impacta sobre el CAPEX y el OPEX. Esto es debido a que se esperan menos reemplazos por componentes rotos y estos a su vez estarán en funcionamiento con los parámetros iniciales.
La producción está marcada por más factores y, entre ellos, uno de los más importantes es el dimensionado del campo solar respecto a las propiedades del emplazamiento. Recordemos que en España todas las plantas se encuentran en estado de “dumping” en los periodos de máxima insolación (mayo – septiembre).
La unión vidrio-metal no resulta imprescindible ya que no se requiere compensar las dilataciones por tubo -basado en el concepto de independencia entre tubo interno y externo-. La expansión total del tubo de acero se compensa con un fuelle al final del semi-colector (fuera del área reflectora), lo que no limita el área efectiva del tubo. Esto supone un ahorro (no existe GTMS) y un incremento de eficiencia.
CSP: ¿Cuál es el coste de aplicación de esta solución a las plantas CSP?
HC: El coste se ha reducido y en ningún caso es superior al de los actuales tubos. La única diferencia entre instalar estos nuevos tubos absorbentes y utilizar los convencionales reside en usar unos brazos distintos cada 6 metros y no cada 4 metros. Por ello, uno de los objetivos clave es repotenciar las plantas a corto plazo, a partir de la utilización de los nuevos tubos.
CSP: ¿El tubo está diseñado pensando en usar sales fundidas como HTF?
HC: El tubo está diseñado para trabajar en todos los rangos operativos y con cualquier fluido térmico. La validación en campo, sin embargo, ha sido realizada con sales fundidas, por ser éste el proceso mejor conocido para trabajar por encima de los 400ºC.
CSP: ¿Se puede usar estos tubos con los actuales aceites de difenilo? ¿Se obtendría alguna mejora técnica y/o económica?
HC: Sí. De hecho este es precisamente el objetivo a corto plazo. La tecnología se basa en la independencia entre tubo interno y externo. Esto implica que la temperatura no es un factor limitante, ni es necesaria la unión con GTMS. La mejora siempre está enfocada en la reducción del precio del kWh, gracias a un componente más fiable, más barato de fabricar y con mayor eficiencia.
CSP: ¿Qué nos puede decir sobre su comercialización, precio y mercado al que va dirigido?
HC: El precio de venta será menor que el de los tubos disponibles en el mercado, ya que por un lado, su coste real de fabricación es menor y por otro, se ensambla en campo sin necesidad de grandes instalaciones fabriles, costes de transporte o seguros asociados. Respecto a los mercados, yo definiría dos: plantas en funcionamiento (con el reemplazo de viejos tubos), y plantas en construcción.
Respecto al reemplazo, la tasa de fallo de los tubos (roturas y pérdidas de vacío) es variable y no es una información pública, pero por la experiencia de Aries Ingeniería, estimamos que podría estar alrededor del 5 %.
Asimismo, cabe destacar que ya contamos con la patente china para el tubo absorbente y las patentes americana, europea y australiana se encuentran en una fase muy avanzada de gestión.
En cuanto a su aplicación en nuevas plantas solares, tendría en cuenta las proyecciones de la Agencia Internacional de la Energía (IEA, por sus siglas en inglés) que consideran un incremento exponencial para la tecnología CSP en los próximos años. Las expectativas, como mínimo, resultan muy interesantes.
Las conclusiones y resultados finales del proyecto se presentaron en el marco del II Seminario HITECO, en la sede de la Agencia Italiana para las Nuevas Tecnologías, Energía y Desarrollo Económico Sostenible (ENEA).
El evento fue organizado por Aries Ingeniería y contó con la participación de empresas del sector, centros de investigación y la comunidad académica y científica.
Las compañías participantes del proyecto son: Aries Ingeniería y Sistemas; ETH Zürich; Asociación de la Industria Navarra; Witzenmann GmbH; Fundación Cidaut; Kavalierglass A.S; Fundación TEKNIKER-IK4; Pfeiffer Vacuum Technology, AG; Instituto de Ciencia de Materiales de Madrid; Trelleborg Sealing Solutions, AB y la ENEA.
La investigación que ha dado lugar a estos resultados ha recibido financiación del Séptimo Programa Marco de la Unión Europea (PM7/2007-2013) en virtud del acuerdo de subvención nº 256830.